Efficient equipment maintenance is critical for manufacturing operations, but unplanned downtime Downtime events can still occur for various reasons. Fortunately, there are strategies you can implement to help reduce unplanned downtime and increase your overall productivity. In this article, we'll explore five effective tips that can help you lower downtime, prevent system outages, and decrease unexpected A significant downtime event can occur due to equipment failure.
Key Takeaways:
- Implementing preventive maintenance is a crucial way to reduce machine downtime. Programs can help minimize unplanned downtime and equipment failure.
- Optimizing Quality control measures can help identify issues that might cause machine downtime. measures are crucial for minimizing downtime and reducing defects.
- Utilizing data analysis and predictive maintenance techniques can significantly reduce downtime.
- Automation plays a key role in reducing downtime and improving overall efficiency.
- Scheduled downtime is crucial for maintaining equipment health and minimizing unexpected breakdowns.
Implement preventive maintenance programs.
Implementing preventive maintenance programs can help you minimize unplanned downtime and equipment failure. By regularly inspecting and servicing machinery, you can identify and address potential issues before they lead to costly breakdowns.
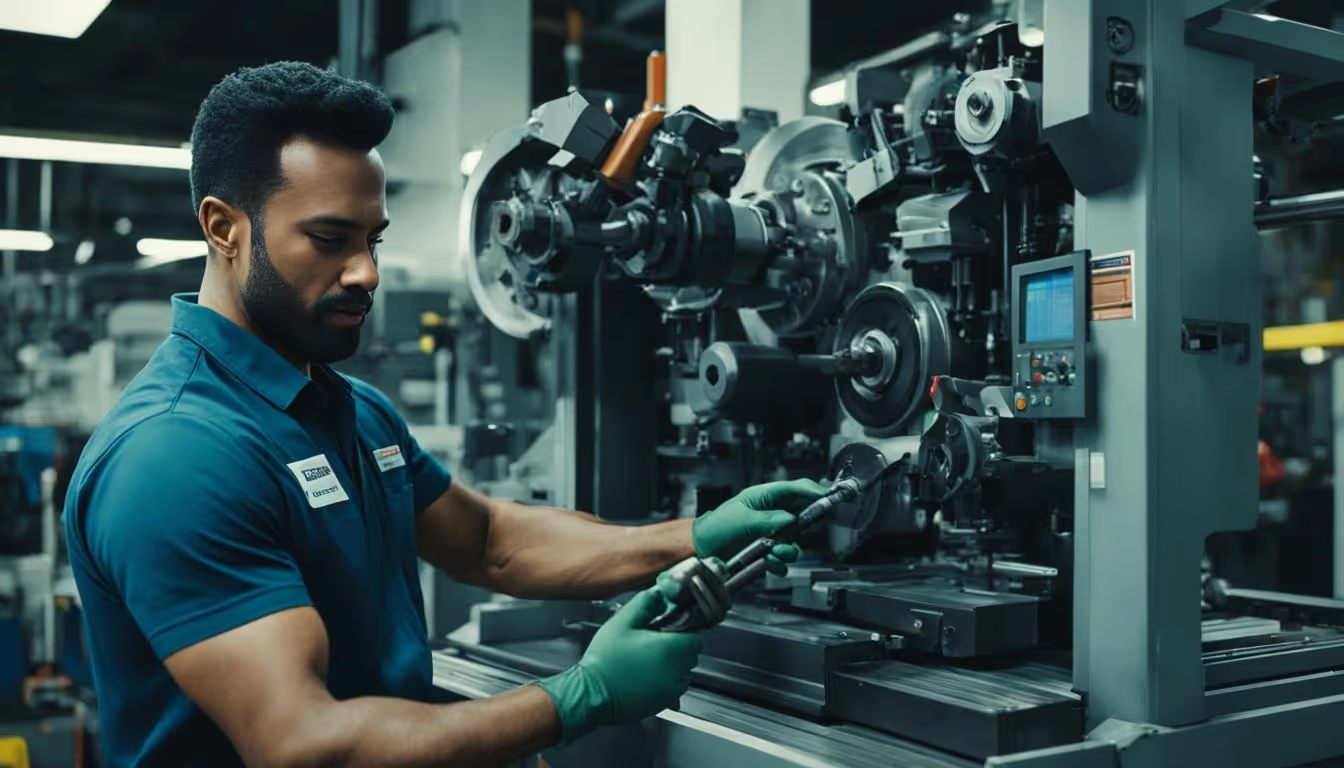
Maintenance software can be effectively used for downtime tracking. can streamline and automate these processes, improving overall efficiency. Software can help you schedule routine maintenance tasks and track equipment performance data, enabling you to make informed decisions and identify patterns that may indicate upcoming issues.
Preventive maintenance is crucial for minimizing unplanned downtime. An effective program can make all the difference in ensuring the ongoing reliability and availability of equipment.
The Benefits of Preventive Maintenance Programs
In addition to reducing downtime, implementing a preventive maintenance program can provide various benefits, such as:
- Increased productivity
- Extended equipment lifespans can result from efforts to reduce machine downtime.
- Higher safety standards
Investing in Your Manufacturing Operation
By investing in a preventive maintenance program and utilizing maintenance software, you can optimize your equipment maintenance and increase overall manufacturing efficiency. Don't wait until equipment failure occurs; be proactive and prioritize maintaining your equipment to minimize downtime.
Optimize quality control measures.
Effective quality control measures are essential to minimize downtime in manufacturing. By implementing strict quality checks at different stages of the production process, you can detect early warning signals, thereby preventing defects that may lead to unwarranted downtime. Consider implementing techniques like statistical process control (SPC), which can help you identify variations in the production process before they result in quality issues.
Another important aspect of quality control is ongoing equipment monitoring. Using sensors to track metrics like temperature and vibration can help you catch problems early and avoid costly downtime.
"Well-executed quality control measures can lower downtime by up to 40–50%." maintenance manager
You should also consider using automated inspection equipment, which can help you take advantage of predictive maintenance programs. By integrating automated inspection equipment with predictive maintenance software, you can identify potential equipment failures and schedule maintenance and repairs at the most opportune times, thereby minimizing downtime.
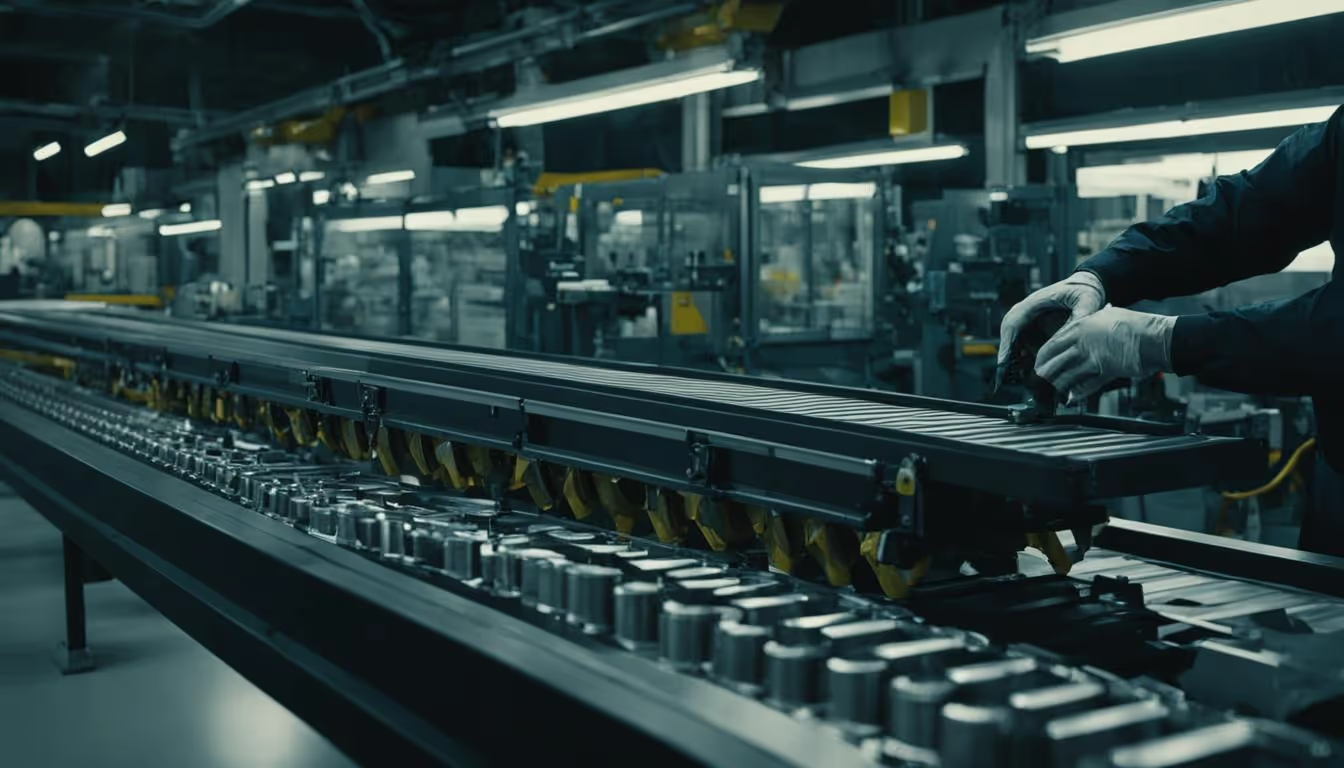
Example Table: Quality Control Checks
It's important to customize your quality control measures according to the specific needs of your operation. Be sure to regularly review and refine them to ensure maximum effectiveness.
Utilize data for predictive maintenance.
Leveraging data analysis can significantly reduce downtime. By monitoring equipment performance and analyzing data patterns, you can identify potential maintenance needs and schedule preventive measures at the most opportune times, optimizing equipment maintenance and minimizing system outages.
Advanced predictive maintenance techniques can take this a step further by anticipating future issues before they occur. Data-driven maintenance strategies, also known as condition-based maintenance, use real-time sensor data to monitor the health of equipment and predict when maintenance will be necessary. This approach maximizes uptime, reduces costs associated with unexpected downtime and repair, and improves the effectiveness of maintenance activities.
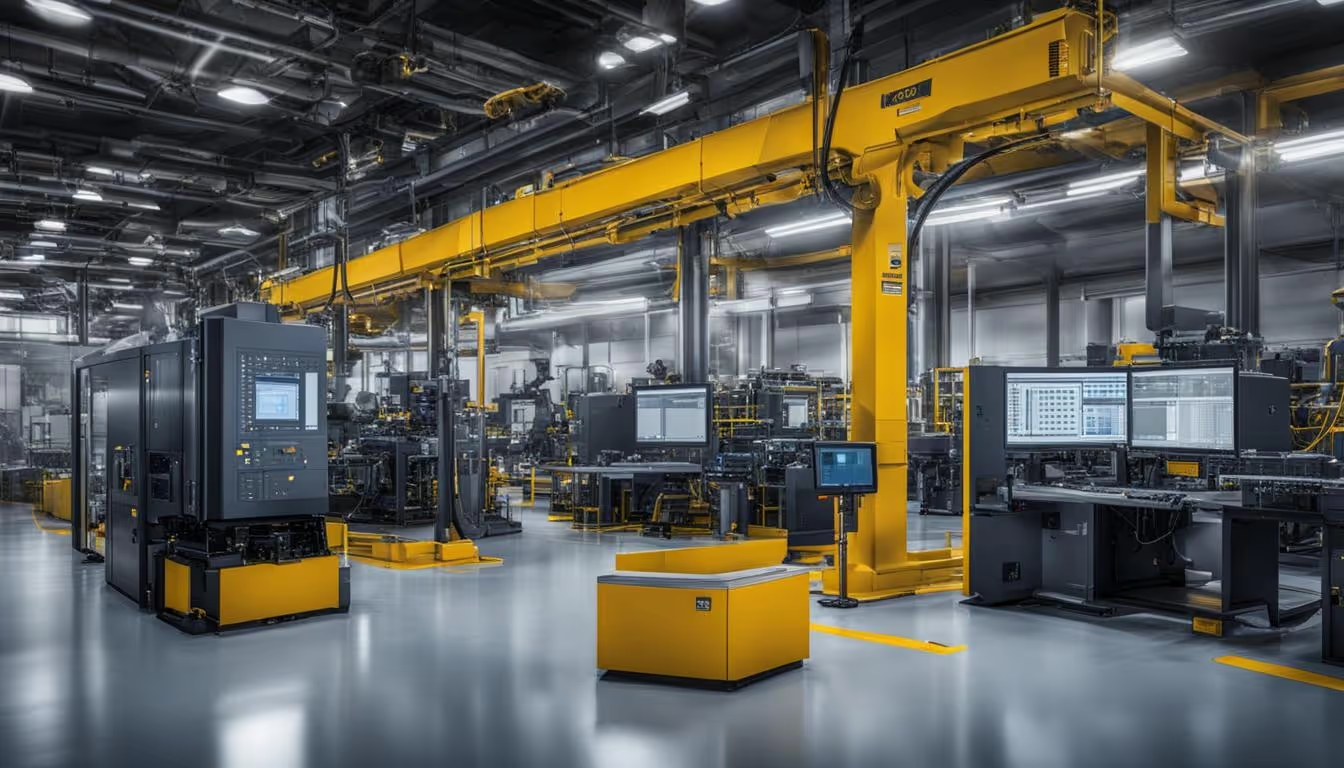
The Benefits of Utilizing Data for Predictive Maintenance
By using data to optimize equipment maintenance, manufacturers can:
- Reduce unplanned downtime.
- Improve equipment reliability to reduce machine downtime.
- Increase safety for workers and machinery.
- Identify critical maintenance needs before equipment failure.
Data analysis enables manufacturers to respond to problems like machine downtime before they escalate, reducing overall downtime and improving the efficiency and availability of equipment.
Automate Processes
One of the most effective ways to decrease downtime is by automating manual processes. By doing so, you can eliminate human error and increase overall efficiency. Automated systems can continuously monitor equipment performance and quickly detect anomalies, allowing you to address potential issues before they cause extended downtime.
Utilizing automated systems can also help improve uptime and increase availability, as you can schedule maintenance or repair actions to occur during low-demand periods, minimizing the impact on production. This is especially useful in cases where manual maintenance would require shutting down entire systems or production lines.
"Automation applied to an inefficient operation will magnify the inefficiency." Plant Manager
Plan and execute scheduled downtime.
Planned downtime is a necessary part of equipment maintenance that can prevent costly and unexpected breakdowns. By scheduling maintenance during low-demand periods, you can minimize the impact on production and ensure that equipment remains in optimal condition. This proactive approach will help you keep your equipment running smoothly and reduce the risk of extended downtime.
During scheduled downtime, it is critical to perform comprehensive equipment checks. A way to reduce unexpected machine downtime includes procedures such as lubrication, tightening, and calibration. This will help you identify any potential issues and address them before they turn into larger problems that can lead to extended downtime. Regular inspections should also include the replacement of critical components, ensuring that your equipment is running at peak efficiency.
Maximizing the Benefits of Planned Downtime
To reduce downtime in your manufacturing, it is essential to have a well-prepared maintenance plan. This plan should include a detailed list of equipment to be serviced, the scope of work, the expected downtime, and the necessary personnel and resources. By having a well-prepared plan in place, you can streamline the maintenance process and minimize the duration of downtime, making the most of the time allocated.
Another way to maximize the benefits of scheduled downtime is by using the time to perform training sessions for your staff. This will help them develop a deeper understanding of the equipment and how to identify potential issues, ensuring that they can handle minor problems before they become larger ones. Staff training can also help increase the efficiency of your team, ensuring that maintenance tasks are performed more effectively and with fewer errors.
Overall, planned downtime is a crucial aspect of maintaining equipment health and reducing the risk of unexpected downtime. By planning and executing maintenance during low-demand periods, you can minimize the disruption to production and ensure that equipment remains in optimal condition.
Conclusion
Implementing these five tips in your manufacturing operation can lead to a significant decrease in downtime and an increase in availability. By regularly implementing preventive maintenance programs, optimizing your quality control measures, utilizing data for predictive maintenance, automating processes, and executing scheduled downtime, your equipment and production will be in optimal condition, leading to improved overall productivity.
Remember, taking proactive measures to reduce downtime not only saves you time and money but also increases customer satisfaction and loyalty. So, apply these strategies now and enjoy the benefits of a more efficient and reliable manufacturing operation.