
Achieving a proactive maintenance culture and increasing plant reliability.
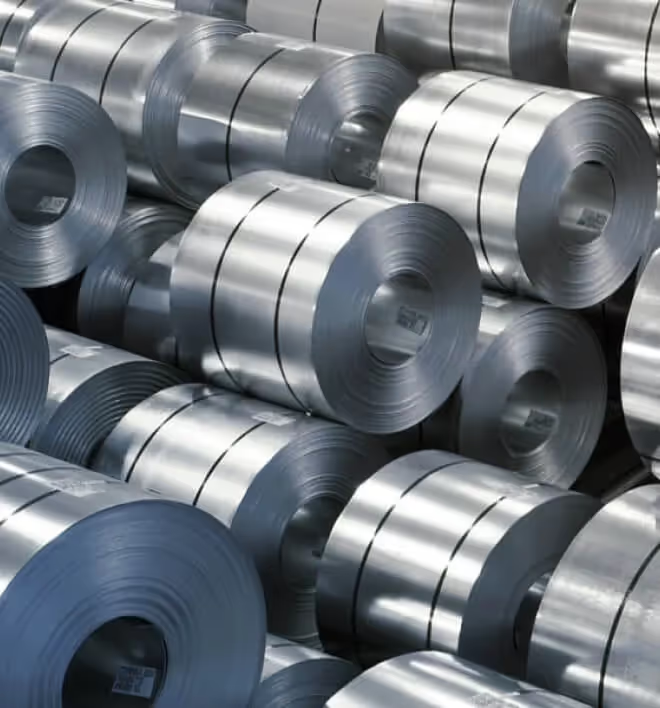
The Challenge
In 2017, Worthington Steel embarked on a maintenance challenge. Their goal was to improve overall plant reliability, and transform their maintenance and reliability division from a reactive culture to a proactive one. It was a visionary look toward the future for the global metals manufacturing company.
The Journey
Following the blueprint of its five-stage Reliability Triangle, with the ultimate goal being to achieve operational excellence and to target 100% machine reliability, Worthington Steel first established and executed a planned maintenance strategy.
But to achieve the next stage, a truly proactive maintenance culture, the company needed an affordable and comprehensive condition-based predictive maintenance solution. That's when Worthington Steel partnered with AssetWatch®.
With the AssetWatch® team responsible for installing and maintaining the wireless condition monitoring system, analyzing machine health data, and providing prescriptive maintenance recommendations, Worthington Steel was empowered with the tools, data and insights needed to make better decisions and the time to proactively schedule maintenance before critical machines fail.
Since partnering with AssetWatch®, Worthington Steel has seen enormous gains from the cultural transformation to proactive maintenance as well as the ongoing financial benefits of saving millions of dollars annually across the 17 plants being monitored by AssetWatch®.
Jeremie Lieb Maintenance Agile Team Lead
Condition based monitoring in action
Within weeks of installation, the Delta Plant had its first big win. We detected a potential failure and suggested a replacement of a furnace roll bearing which prevented approximately 48 hours of unplanned downtime and $500k in potential lost gross margin.
How much could you save by using AssetWatch?
Get Started TodayFind this case study helpful? We’d love to share it with you!
AssetWatch partnered with AWS to provide the scalability and reliability needed to support a serverless architecture. With a robust suite of services tailored for data ingestion, processing, and machine learning, AWS enables AssetWatch to seamlessly scale sensor data and deliver predictive insights to manufacturing companies. AWS infrastructure reduces operational overhead and allows AssetWatch to focus on innovation to drive value to our customers. Additionally, AWS’s strong security framework and global infrastructure ensure the resilience and compliance required to support mission-critical manufacturing operations at scale. This partnership positions AssetWatch to accelerate growth while maintaining the highest levels of performance and reliability.
.avif)

How much could you save by using AssetWatch?
Really Great Results
After initially deploying Vero® at its flagship steel processing facility in Columbus, OH, Worthington Steel expanded the proactive maintenance system across their enterprise. In total, more than 1,800 vibration+temperature sensors are now tracking the health of 650+ critical machine assets at 17 steel processing and pressure cylinder facilities located throughout North America.
Since the first installation, more than eight million full-spectrum vibration and temperature readings have been gathered by Vero® sensors and delivered to AssetWatch® for processing and visualization on its cloud-based software platform. Assisted by machine learning, expert Condition Monitoring Engineers (CMEs) have analyzed the data and have issued more than 400 prescriptive maintenance recommendations.
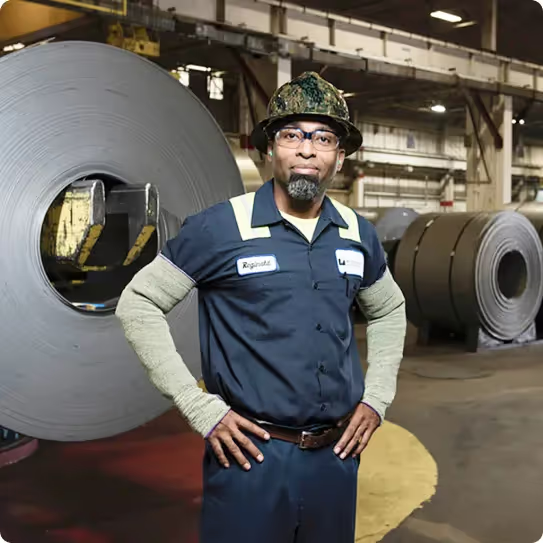
“Worthington Steel is a global leader in its field, but we needed a solution that was outside our purview. We sought out a partner that had specialized expertise.”
Brad Kern, VP, Steel Operations
Our 30-day, risk free trial is only $199.
AssetWatch customers save on average 8x in ROI. That means for every $1 you give us, we give $8 back to you.
Includes professional installation of up to 200 sensors (a $10k+ value)
24/7 monitoring and a dedicated CME for your site
AssetWatch cloud-based software with unlimited licenses
No CapEx, Engineering or IT integration required