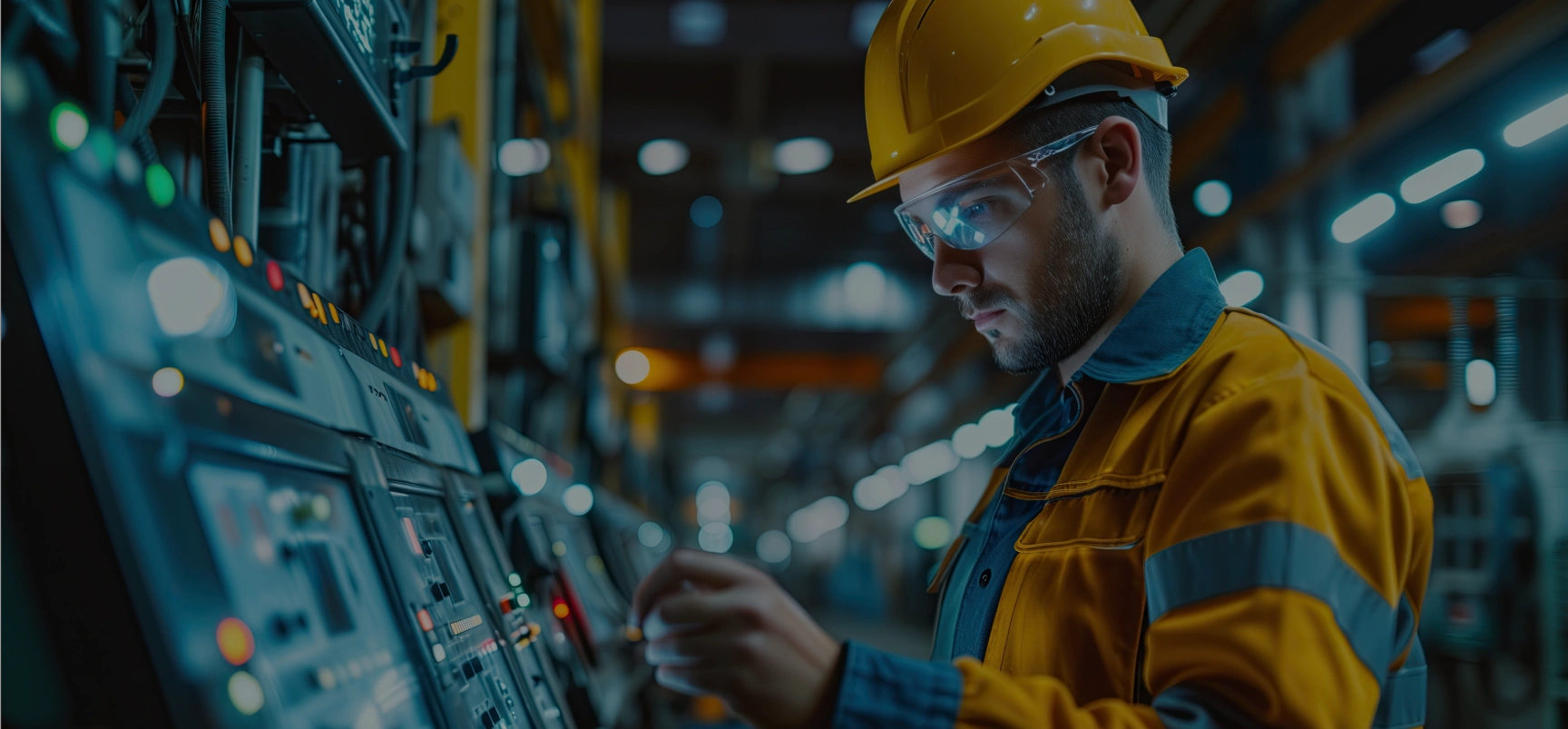
Transform Your Plastics Manufacturing Process
Increase Productivity and Lower Costs with our Predictive Maintenance Solution for the Plastics Industry
Transform Your Plastics Manufacturing Process
Increase Productivity and Lower Costs with our Predictive Maintenance Solution for the Plastics Industry
Transform Your Plastics Manufacturing Process
Increase Productivity and Lower Costs with our Predictive Maintenance Solution for the Plastics Industry
Optimize Your Operations with Advanced Prescriptive Maintenance for the Plastics Industry
In the plastics manufacturing industry, maintenance and reliability teams grapple with numerous challenges, including maintaining the efficiency and reliability of critical equipment such as extruders, injection molding machines, and conveyors. These machines are essential for ensuring consistent product quality and high production output. However, the complexity of plastic processing, coupled with the need for precise temperature and pressure control, makes this a demanding task. Frequent equipment failures can lead to costly downtime, reduced productivity, and increased maintenance costs.
AssetWatch offers a premier end-to-end remote condition monitoring solution specifically designed to address these challenges. By continuously monitoring the health and performance of critical equipment, AssetWatch provides real-time data and predictive insights that enable proactive maintenance. This not only helps prevent unexpected breakdowns but also optimizes equipment performance, ensuring smooth and efficient operations.
With AssetWatch, your maintenance team gains a reliable partner dedicated to enhancing operational efficiency, ensuring product quality, and minimizing downtime in the demanding landscape of the plastics manufacturing industry.
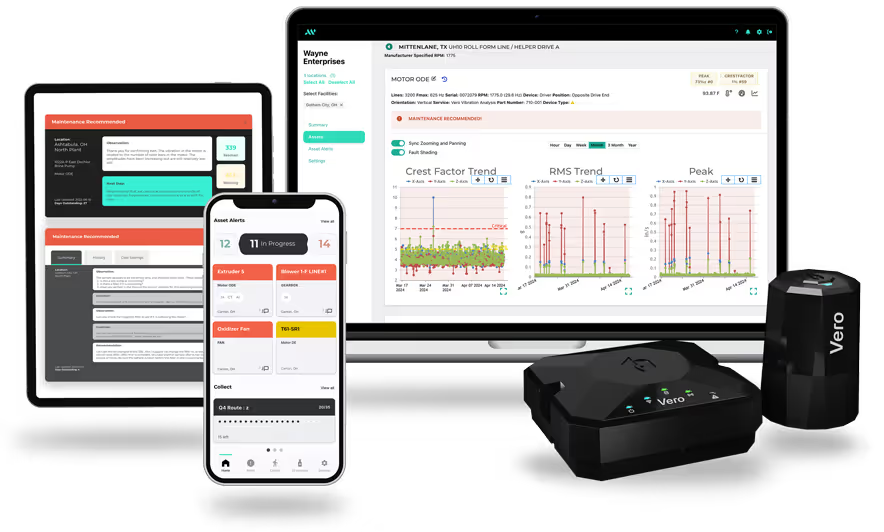
Manufacturing Challenges
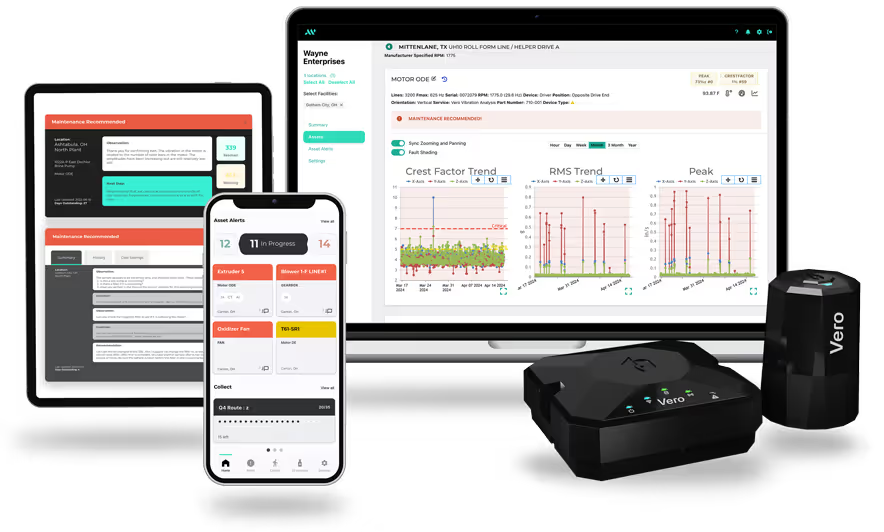
Manufacturing Challenges
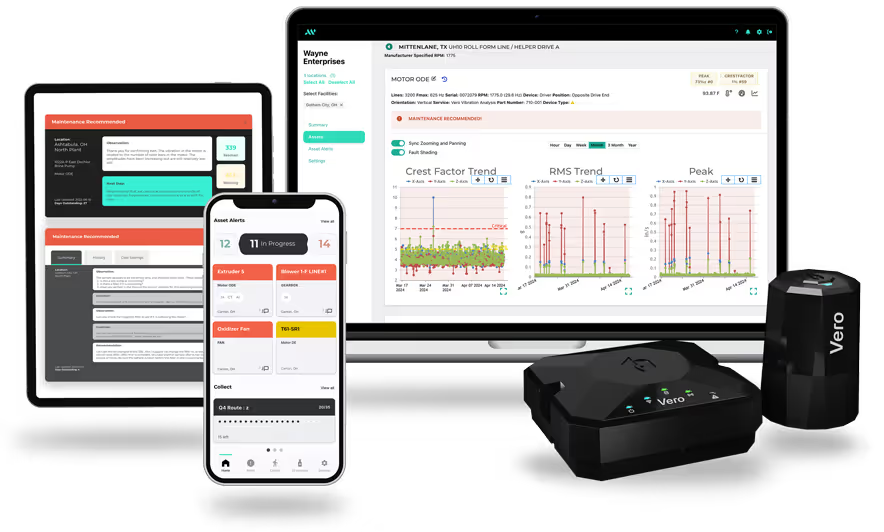
Manufacturing Challenges
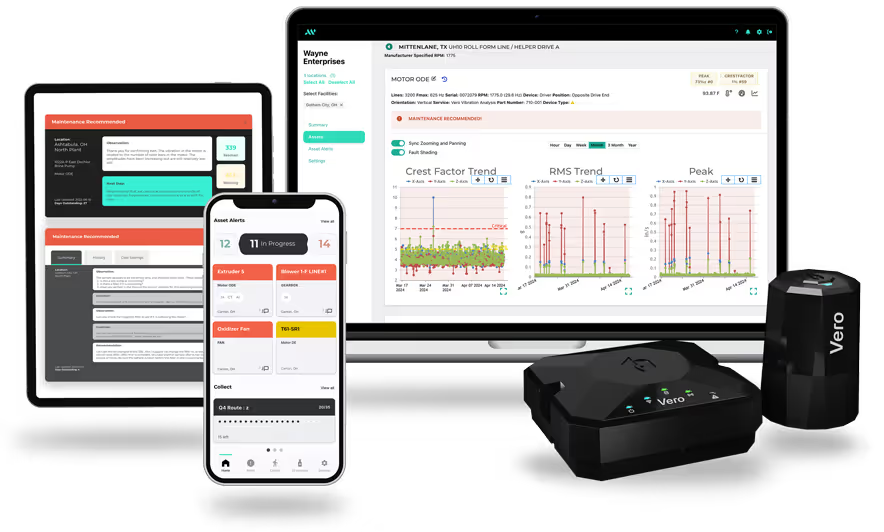
Manufacturing Challenges
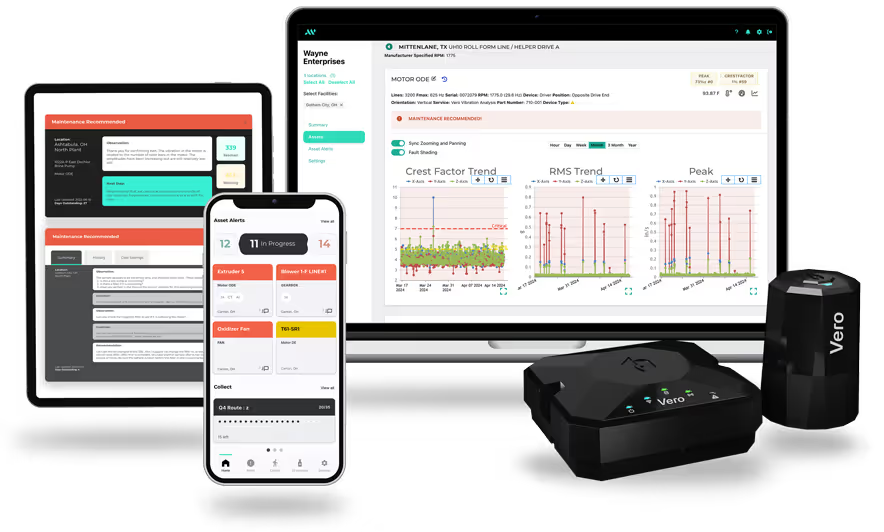
Manufacturing Challenges
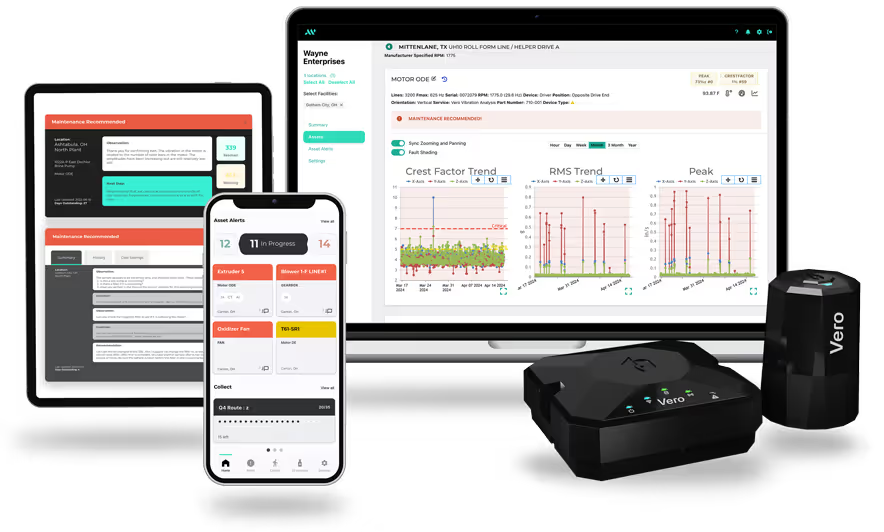
Manufacturing Challenges
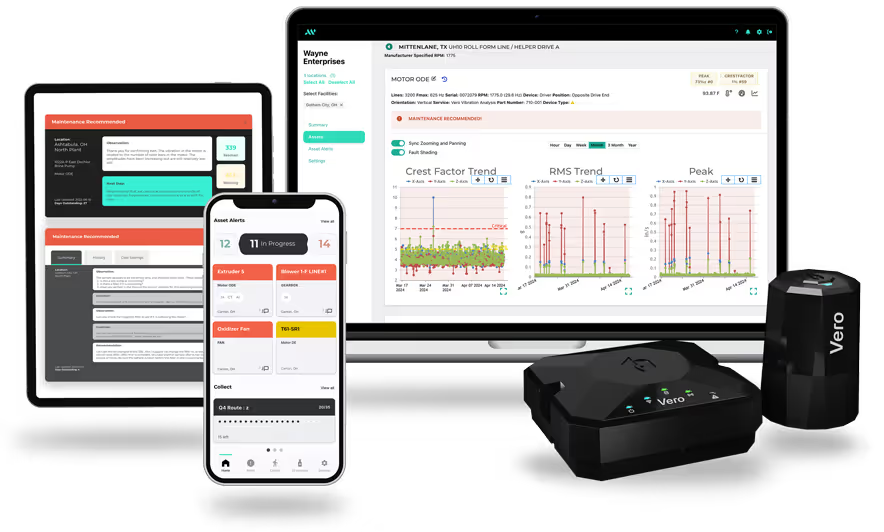
Manufacturing Challenges
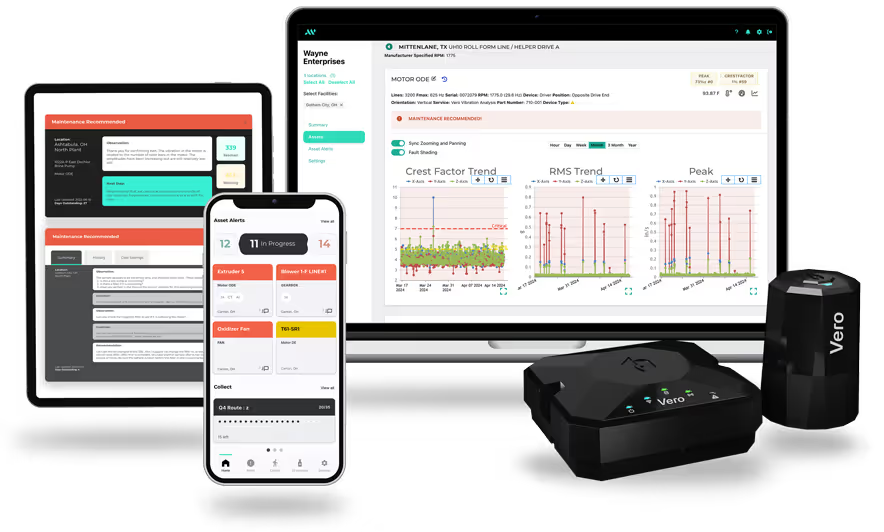
Manufacturing Challenges
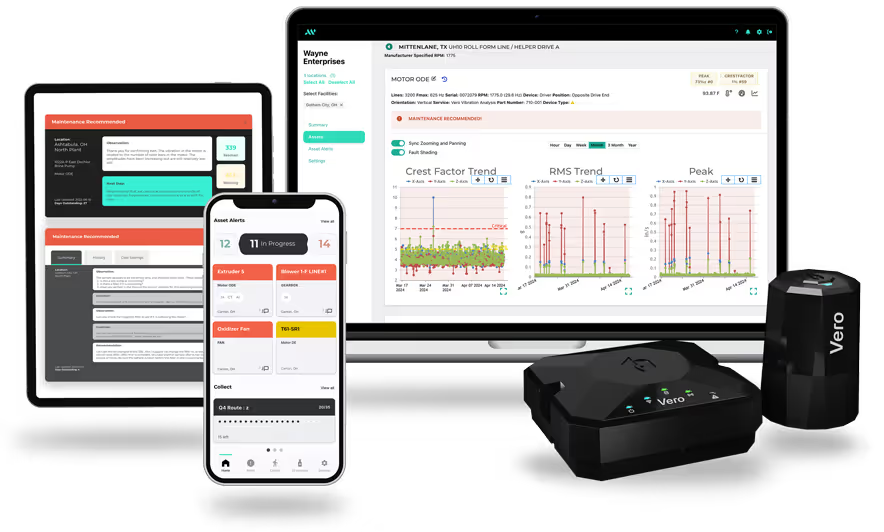
Manufacturing Challenges
Our growth continues as we partner with more customers to eliminate unplanned downtime in the plastics industry.
Plastics manufacturers have streamlined their operations by leveraging our advanced predictive maintenance solution, achieving substantial financial and operational gains.
“I have had great experience with my CME. We have been able to successfully repair / replace multiple gearboxes, motors, pumps, and even DC drive parts due to the info he was able to provide before the failure could cause downtime. I would recommend all plants use this service and take it seriously.”
“With the CME, I feel like I have a highly qualified tech on my team. I am not bombarded by alerts, I appreciate the conversations.”
“With the CME, I feel like I have a highly qualified tech on my team. I am not bombarded by alerts, I appreciate the conversations.”
“Vero sensors and insight from our AssetWatch CME saved us an estimated $1.2M in just one year. My team and leadership quickly went from skeptical to having a fear of going without Vero in a very short time.”
“I have had great experience with my CME. We have been able to successfully repair / replace multiple gearboxes, motors, pumps, and even DC drive parts due to the info he was able to provide before the failure could cause downtime. I would recommend all plants use this service and take it seriously.”
“I have had great experience with my CME. We have been able to successfully repair / replace multiple gearboxes, motors, pumps, and even DC drive parts due to the info he was able to provide before the failure could cause downtime. I would recommend all plants use this service and take it seriously.”
Top 5 Faults Detected
In the plastics industry, early detection of faults enables proactive effort to address issues in the least expensive way, eliminating unplanned downtime and reducing costs.
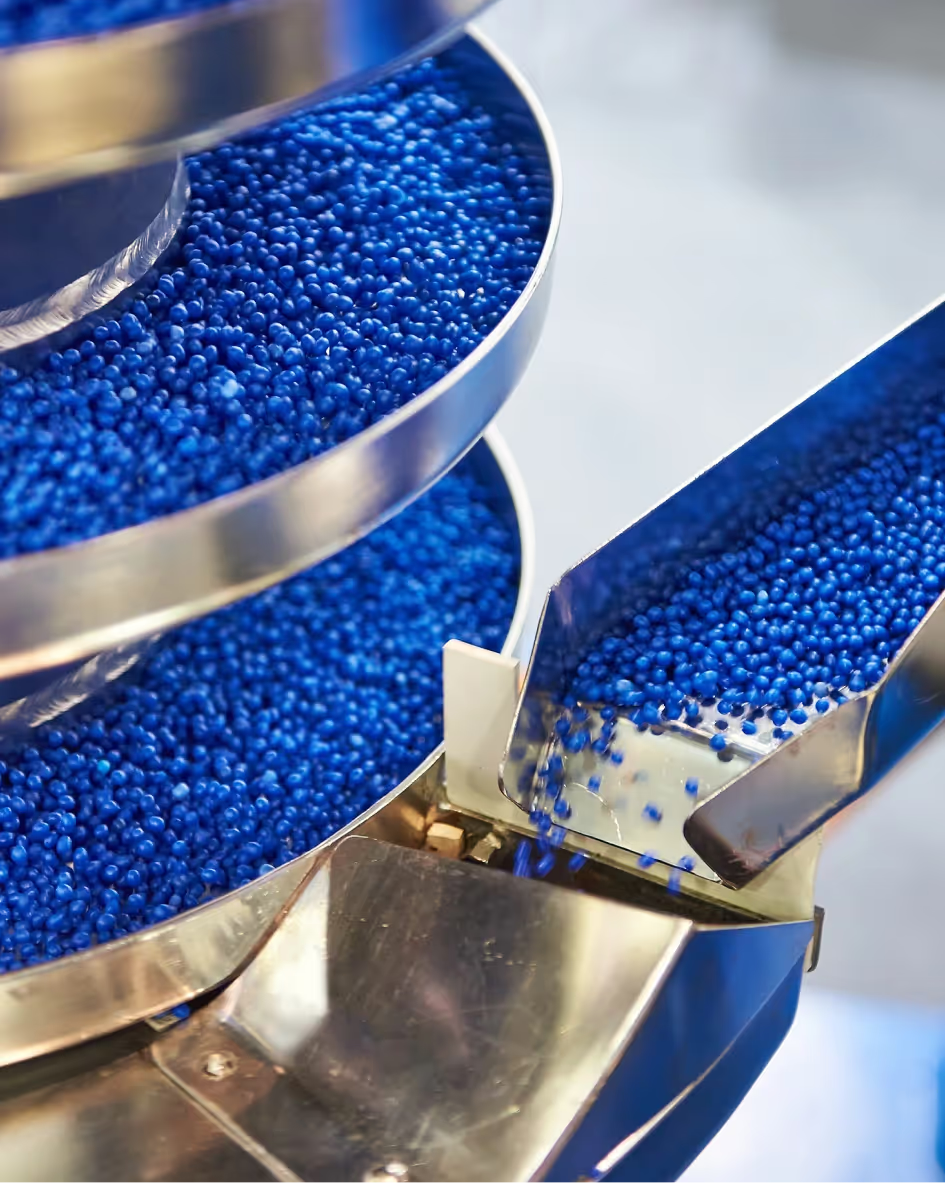
Meet the CME Leadership Team
Real People Providing Real Maintenance Solutions
Power your success with insights and recommendations from one of our many dedicated CAT III/IV certified vibration analysts.
.avif)
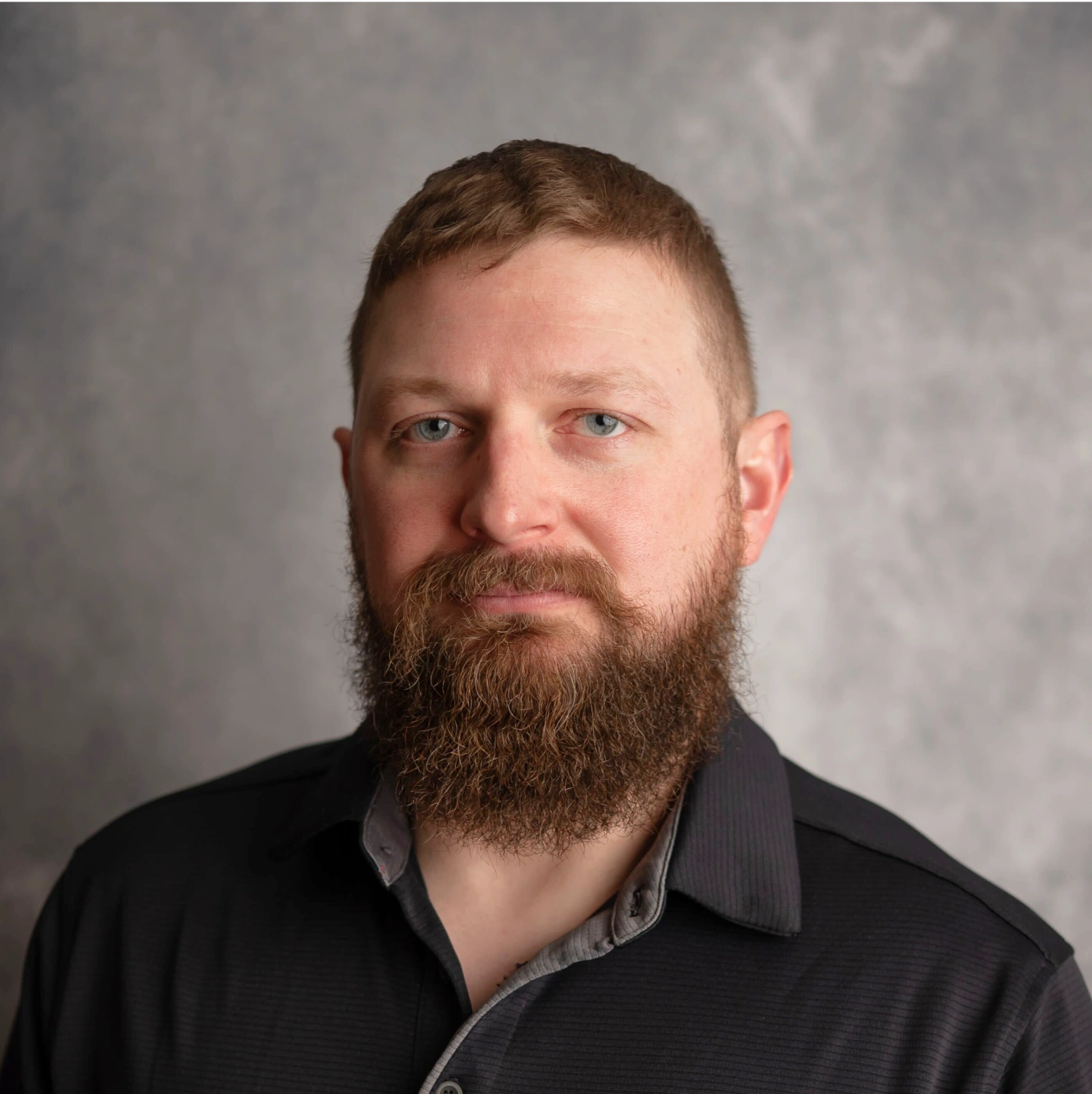
.avif)
.avif)
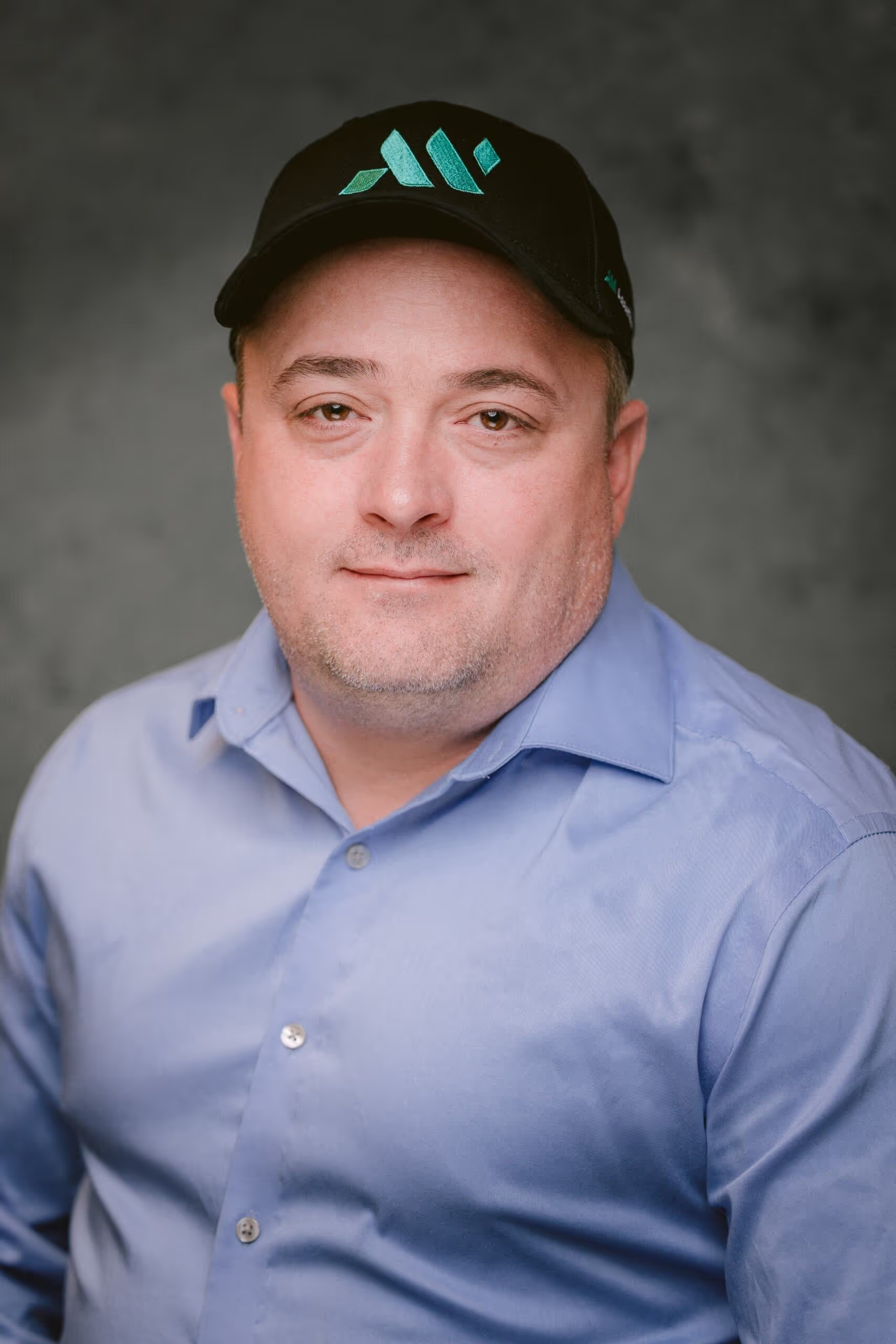
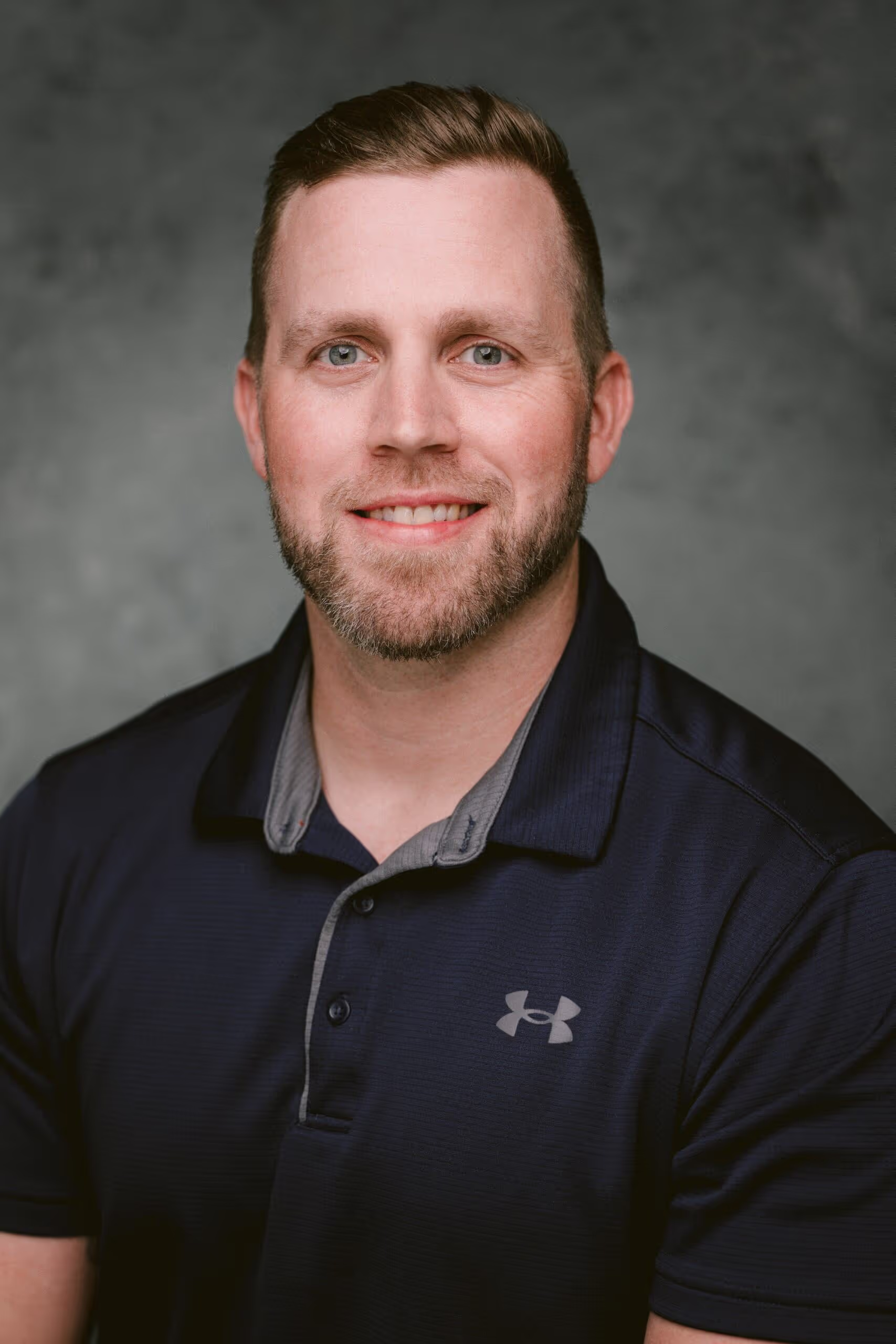
Nationwide Support With A Local Touch
Proudly servicing all locations in the US & Canada
Multiple site visits per year included, ensuring fast, reliable service when you need it most
Professional install by our in-house Reliability Technicians
Our locally based Asset Reliability Technicians are strategically positioned across 83% of all major U.S. cities
Team of dedicated CAT 3 or 4 Vibration Analysts for each site included with program

We Keep Your Assets Running
Our continuous condition monitoring solution and industry knowledge ensure uninterrupted plastics manufacturing for these assets and many more.
See AssetWatch In Action
Minimal Effort, Maximum Savings.
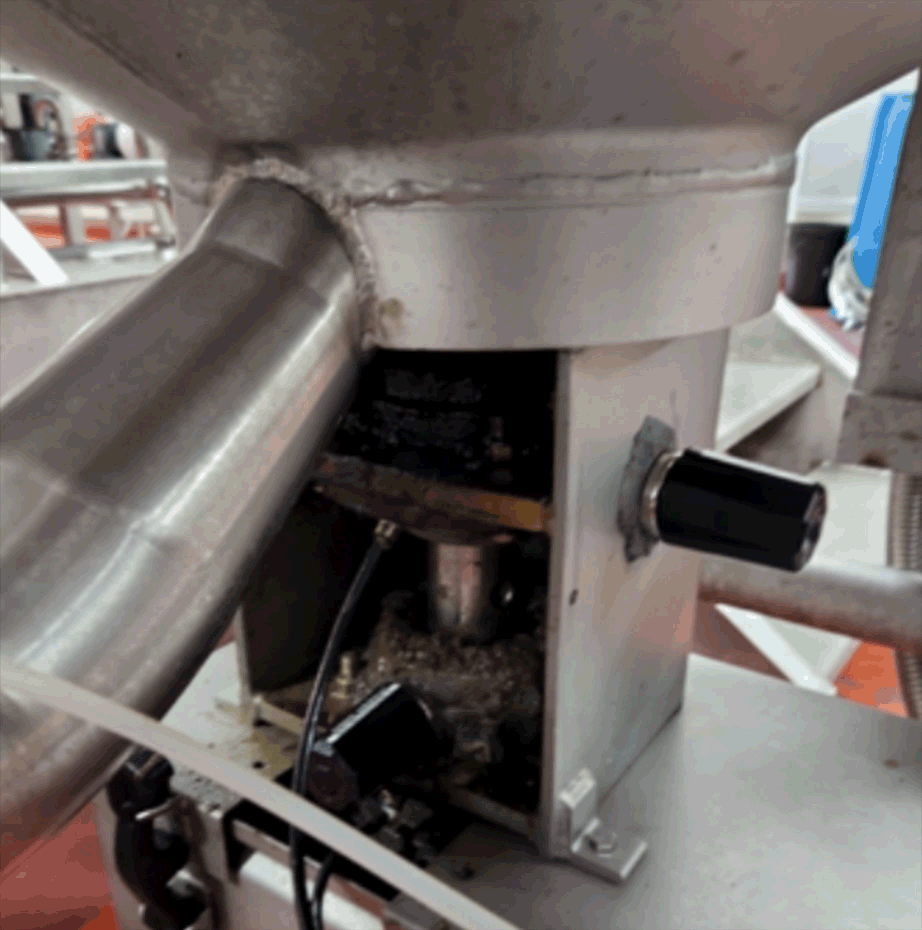
Condition monitoring detected vibrations in an agitator, enabling early replacement of the taper lock and bearings to prevent failure.
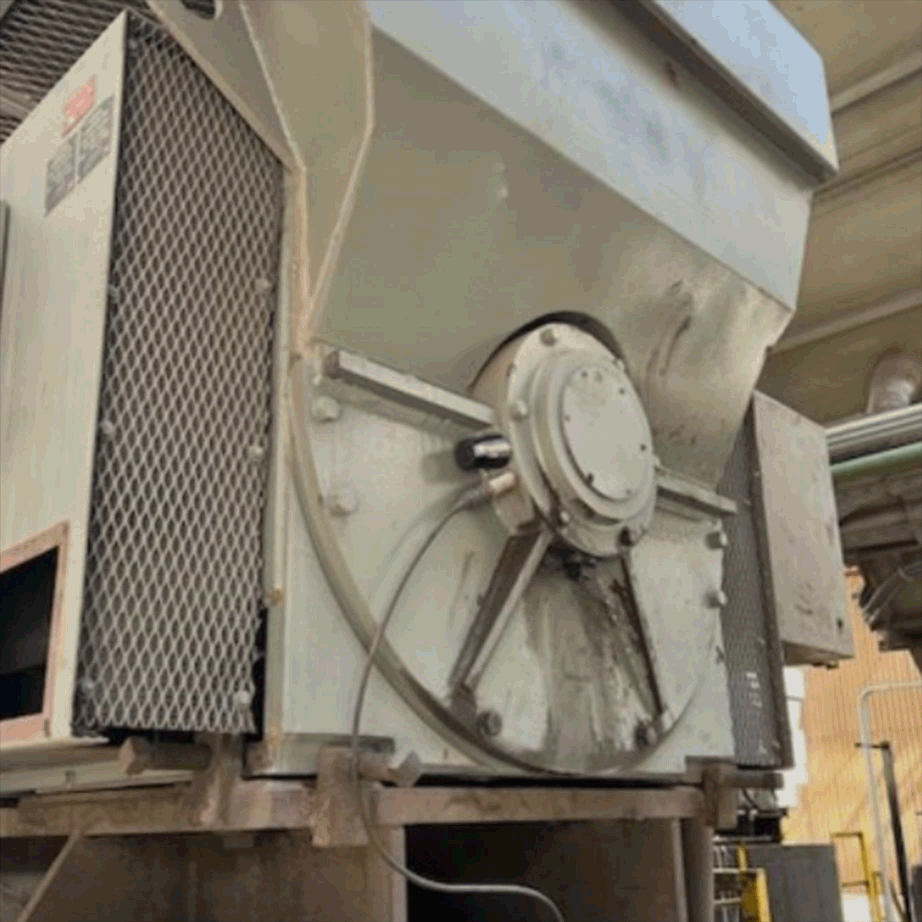
Vero sensors and AssetWatch certified CME detected electrical issues, allowing for preemptive motor replacement.
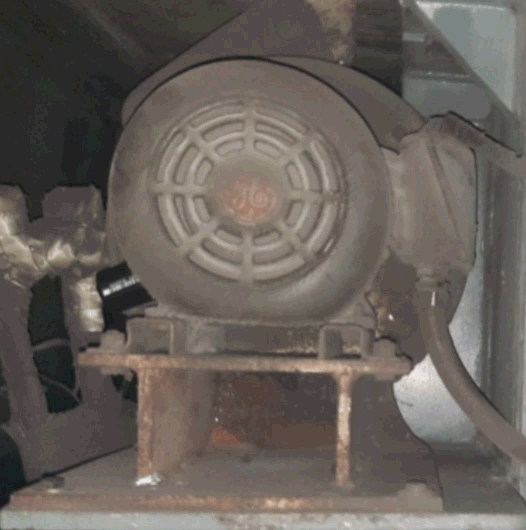
AI detected excessive fan looseness, prompting the replacement of worn components and preventing further damage.
Book a demo

Case Studies
These teams are rockstars in their organizations and we celebrate their work.