If you're looking to maximize uptime and optimize performance in the oil and gas industry, predictive maintenance is a game-changer. By leveraging advanced analytics and machine learning algorithms, predictive maintenance empowers companies to detect issues before they become full-blown problems, minimizing downtime and reducing maintenance expenses.
In this article, we'll explore the importance of predictive maintenance in the oil and gas sector and highlight the benefits it offers in improving efficiency, productivity, safety, and environmental sustainability. We'll also examine real-world use cases and the solutions available for implementing predictive maintenance in your operations.
Key Takeaways:
- Predictive maintenance empowers companies to detect issues before they become costly problems.
- Implementing predictive maintenance can significantly enhance uptime and reduce maintenance expenses.
- Real-world use cases illustrate the benefits of adopting predictive maintenance in the oil and gas industry.
- Advanced analytics, machine learning algorithms, and specialized software solutions are available for implementing predictive maintenance.
- Predictive maintenance is a proactive approach that can help pave the way for a seamless energy future.
Understanding Predictive Maintenance in Oil and Gas Operations
Predictive maintenance is a proactive maintenance strategy that utilizes data analytics and machine learning to optimize equipment performance and avoid unplanned downtime. This approach is gaining increasing popularity in the oil and gas industry due to its ability to enhance efficiency, productivity, and safety.
Predictive maintenance differs from preventative maintenance in that it leverages real-time data and historical performance information to predict when maintenance is required, enabling companies to take corrective action before equipment failure occurs. This minimizes both repair costs and downtime, maximizes system uptime, and ultimately reduces overall maintenance expenses.
The benefits of maintenance in oil and gas operations are numerous. By accurately predicting equipment failures, companies can optimize maintenance schedules, reduce the costs of maintenance activities, and improve overall productivity. In addition, predictive maintenance improves safety by ensuring that equipment issues are identified and addressed before accidents can occur.
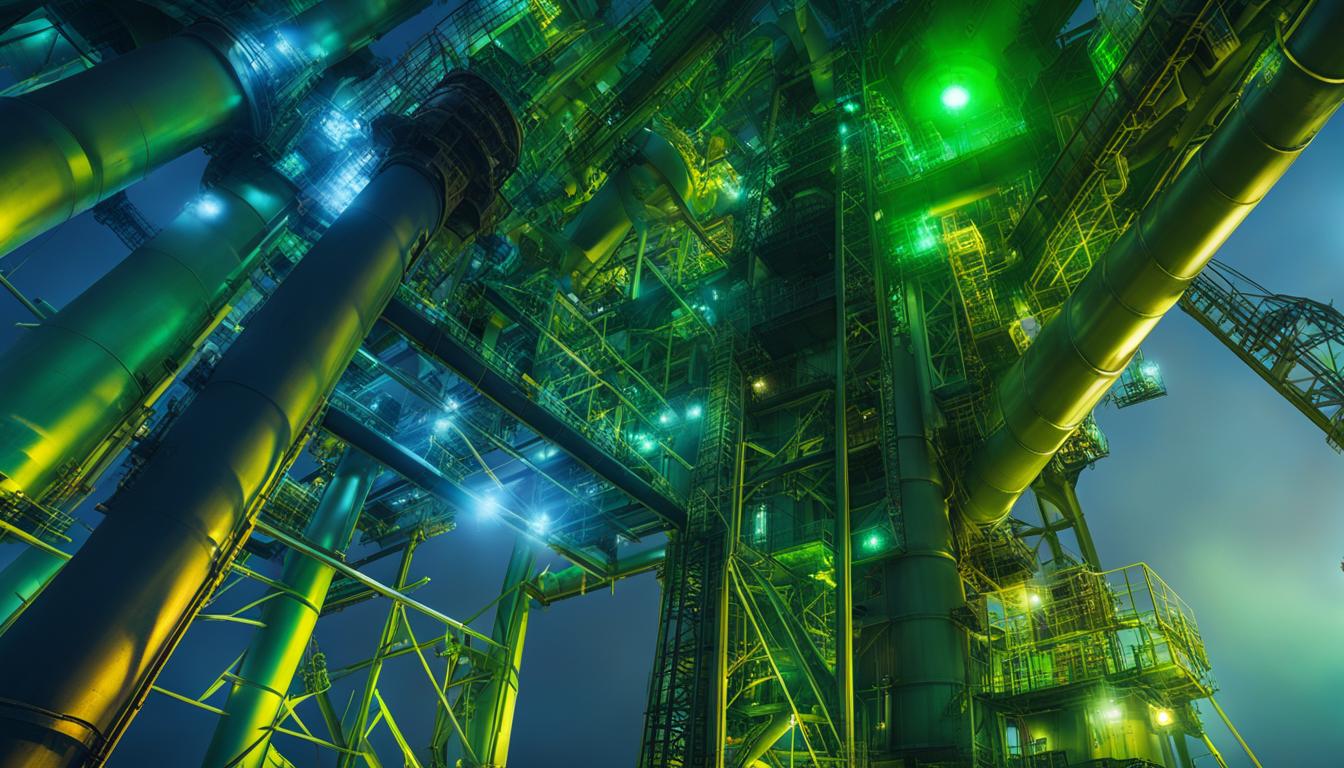
Benefits of Predictive Maintenance over Preventative Maintenance
Predictive maintenance has several techniques, tools, and software available that can be integrated into existing operations. In the next section, we will discuss the process of implementing predictive maintenance.
Implementation of Predictive Maintenance in the Oil and Gas Industry
Integrating predictive maintenance into your oil and gas operations can seem daunting, but with the right tools and techniques, it can be a smooth process. The first step is to assess your current operations and identify areas that could benefit from predictive maintenance.
One effective approach is to use condition monitoring, which involves regularly monitoring equipment and systems to detect any potential issues. Using advanced sensors and analytics software, you can track key metrics such as temperature, pressure, and vibration to quickly identify any anomalies. This approach allows you to take proactive measures to address any issues before they turn into costly downtime or major repairs.
Another useful technique for implementing predictive maintenance is reliability-centered maintenance (RCM), which involves analyzing your equipment to determine the likelihood and impact of potential failures. With this information, you can prioritize maintenance activities and optimize your maintenance strategy for maximum efficiency and uptime.
Furthermore, utilizing machine learning algorithms can also greatly enhance your predictive maintenance capabilities. By training algorithms on historical equipment data, you can predict failures and determine optimal maintenance intervals to reduce downtime and improve overall performance.
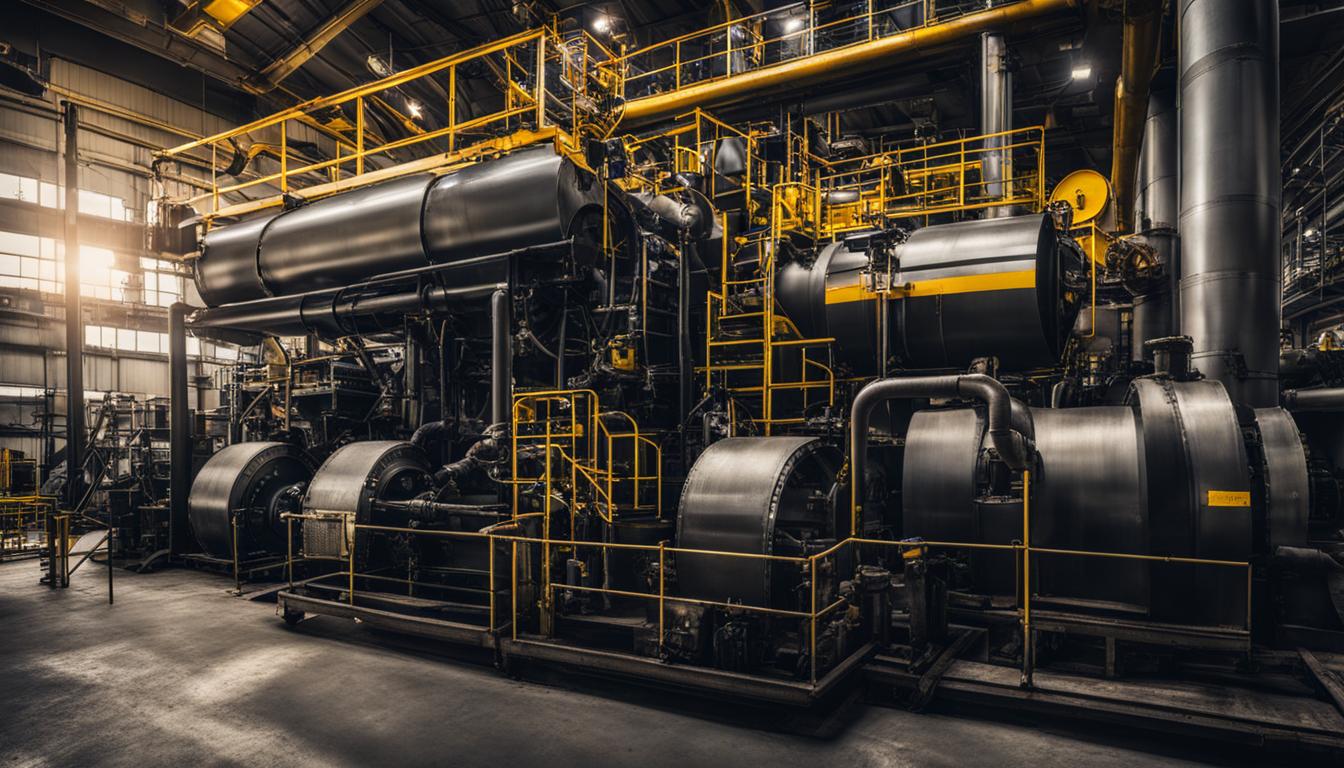
Implementing predictive maintenance can be further aided by investing in specialized predictive maintenance software. These software solutions can simplify and automate many aspects of your predictive maintenance program, from analyzing data to generating work orders.
Overall, by implementing predictive maintenance in your operations, you can significantly improve equipment uptime, reduce costs, and enhance safety. Utilizing techniques such as condition monitoring, RCM, and machine learning, in combination with advanced predictive maintenance software, can optimize your operations and ensure future success.
Benefits of Predictive Maintenance in Oil and Gas
Adopting predictive maintenance can bring about several benefits for your oil and gas operations.
Reduced Downtime
Predictive maintenance uses real-time data to monitor equipment and detect any potential issues, allowing you to address them before they cause downtime. This approach can result in a significant reduction in unscheduled downtime, saving you time and money.
Lowered Operating Costs
Predictive maintenance can help you optimize how you schedule maintenance activities, ensuring that you are not spending more than necessary to maintain your equipment. By being proactive and addressing issues before they become major problems, you can reduce the need for costly repairs and replacements.
Improved Safety
By identifying potential equipment failures before they occur, predictive maintenance can help improve the safety of your operations. This approach reduces the risk of accidents, injuries, and other safety incidents.
Enhanced environmental sustainability
Predictive maintenance allows you to track equipment performance and efficiency, helping you identify areas where you can improve energy usage and reduce waste. This approach leads to more sustainable operations, which can have a meaningful impact on the environment and your bottom line.
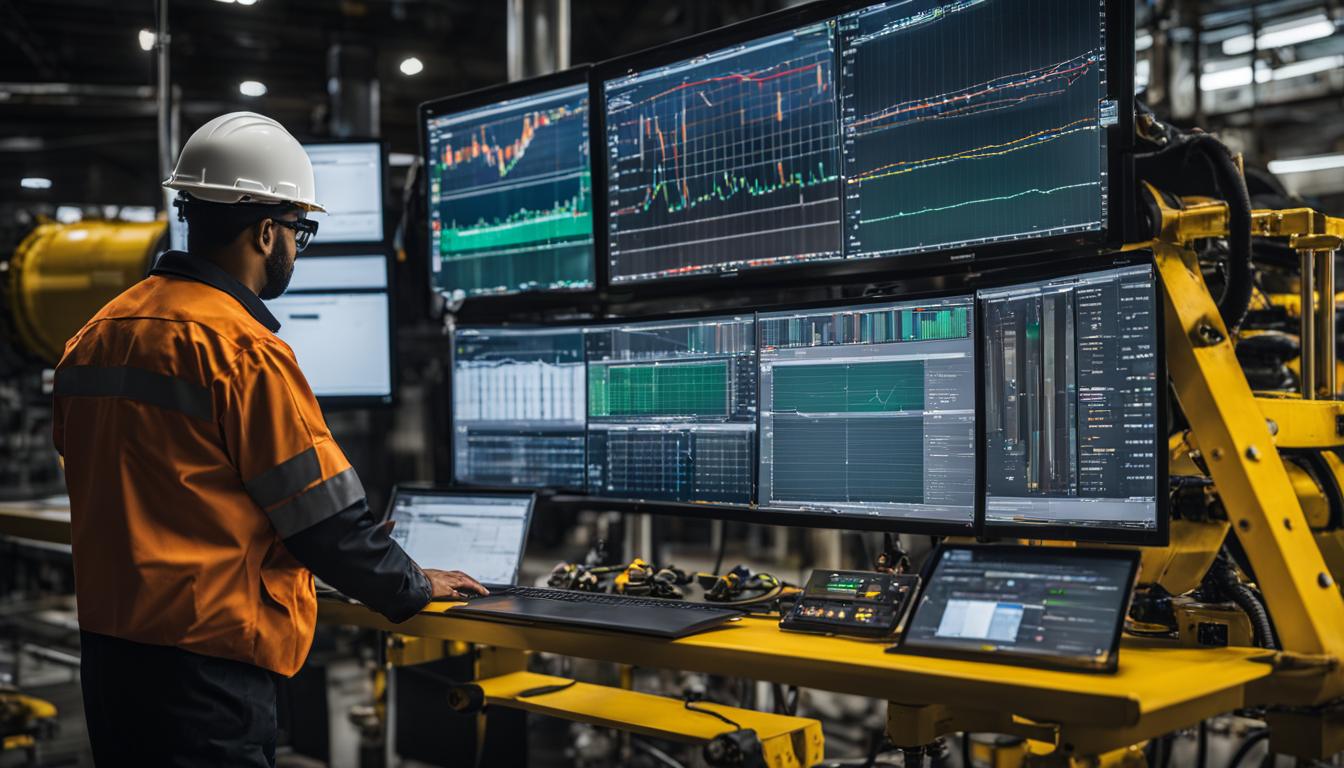
"Predictive maintenance can also improve the overall reliability of your equipment, which can help avoid any lost production costs." Maintenance Engineer, Oil & Gas Industry Expert
Predictive Maintenance Use Cases in Oil and Gas
Implementing predictive maintenance has proven to be highly effective in optimizing operations, ensuring safety, and maintaining a competitive edge. Let's explore some real-world examples of predictive maintenance use cases in the oil and gas industry:
1. Condition-Based Maintenance (CBM)
CBM uses real-time data and condition parameters to predict equipment failure and implement timely repairs before the asset breaks down. Companies have successfully applied CBM to oil rig equipment, reducing downtime, increasing safety, and saving millions per year.
2. Pipeline Monitoring and Inspection
Predictive maintenance techniques are also being used to monitor and inspect pipelines accurately, avoiding leaks and accidents proactively. Certain companies have developed a pipeline monitoring system that uses big data to identify potential weaknesses and proactively repair them, reducing maintenance costs by a significant amount.
3. Electrical Component Monitoring
Many companies are using maintenance to monitor electrical components in various applications, from upstream offshore platforms to natural gas processing plants. With predictive analytics, companies can monitor electrical assets' health, predict failures, and perform maintenance proactively, potentially reducing downtime and maintenance costs by 30–50%.
4. Offshore Oil Platform Monitoring
Offshore oil drilling and production platforms represent some of the most significant investments in the oil and gas industry. Maintenance tools are helping companies better understand equipment health, efficiency, and performance. Some companies have adopted predictive maintenance to monitor their offshore platforms' subsea equipment, improving reliability, reducing maintenance costs by roughly 20–35%, and preprocessing data that can potentially achieve up to 80–95% accuracy in predicting equipment failures.
By implementing predictive maintenance, companies can identify problems before they happen, prevent equipment breakdowns, and save billions of dollars in maintenance costs and wasted resources. By utilizing state-of-the-art technologies, the industry can keep operations running safely and efficiently for years to come.
Predictive Maintenance Solutions for the Oil and Gas Industry
If you're looking to optimize operations and maximize equipment uptime, implementing predictive maintenance solutions for oil and gas is a must. Fortunately, there is no shortage of maintenance tools for oil and gas that can help you achieve these goals.
To get started, you can utilize advanced predictive maintenance software for oil and gas, which relies on algorithms and machine learning to detect anomalies, identify issues before they occur, and generate actionable insights. This software can work with existing data from sensors and other systems, making it seamless to integrate into your operations.
Another effective technique is vibration analysis, which can detect any changes in machinery vibration patterns that could indicate problems and impending failures. This is done using specialized maintenance techniques in oil and gas such as tachometers, accelerometers, and proximity probes, which are used to measure and analyze vibration levels and frequencies.
Overall, taking advantage of maintenance tools and techniques in oil and gas can help you avoid unexpected downtime, minimize maintenance expenses, and ultimately contribute to a more reliable energy future.
Conclusion
Overall, it's clear that adopting maintenance is essential for ensuring better uptime, safety, and efficiency. By predicting potential issues before they occur, you can avoid costly downtime, reduce maintenance expenses, and improve overall productivity.
Not only that, but predictive maintenance also enables companies to enhance their safety measures and reduce the impact of their operations on the environment. By leveraging advanced analytics, machine learning algorithms, and specialized software, you can optimize your operations and pave the way for a seamless energy future.
In conclusion, the importance of maintenance in oil and gas cannot be overstated. By embracing this proactive approach to maintenance and staying ahead of potential issues, you can ensure that your operations run smoothly and efficiently while also reducing costs and minimizing your environmental impact. So, if you haven't already, it's time to explore the benefits of predictive maintenance and implement it into your operations.