In the industrial sector, it is important to keep your machinery and systems running at optimal levels. One of the most effective ways to achieve this is by implementing a preventive maintenance task procedure. Regular maintenance checks and proactive measures can help prevent costly breakdowns, reduce downtime, and ensure maximum equipment efficiency.
Key Takeaways
- A preventive maintenance system is critical for ensuring equipment reliability and efficiency.
- The best practices for creating a preventive maintenance plan involve creating a maintenance schedule, using maintenance software, and implementing a comprehensive program.
- The key components of a preventive maintenance procedure include well-defined maintenance procedures and a comprehensive maintenance checklist.
- Integrating predictive maintenance techniques into your preventive maintenance structure can provide further benefits.
- A well-executed preventive maintenance program can significantly enhance equipment reliability and efficiency.
Understanding preventive maintenance
Preventive maintenance is a proactive approach to equipment maintenance that involves regular inspections, cleaning, lubrication, and adjustments to prevent equipment failure and downtime. There are maintenance management plans that include preventive maintenance tasks. There are different types of preventive maintenance, including corrective maintenance, reactive maintenance, and preventive maintenance checklists.
- Calendar-based maintenance: This type of preventive maintenance is based on a fixed schedule, where maintenance tasks are performed at predefined intervals, regardless of equipment condition. It is commonly used for simple and easily accessible equipment components, such as filters and belts.
- Condition-based maintenance: This type of preventive maintenance relies on equipment condition monitoring to identify maintenance needs. It involves measuring equipment parameters, such as temperature, pressure, and vibration, to detect abnormalities and predict possible failures. Condition-based maintenance management allows for a more accurate and efficient preventive maintenance checklist. Maintenance program, reducing unnecessary maintenance and repair costs.
- Predictive maintenance: This preventive maintenance type uses machine learning algorithms, artificial intelligence, and data analysis to predict equipment failure and maintenance needs. It involves capturing real-time data from sensors or equipment monitors and analyzing it for patterns and anomalies, which can then be used to set up a preventive maintenance schedule. Predictive maintenance The preventive maintenance task enables timely and comprehensive maintenance while reducing equipment downtime and corrective maintenance costs.
Adopting a preventive maintenance approach offers many advantages, including:
- Reduced downtime: Regular maintenance minimizes the risk of equipment failure and downtime, ensuring a consistent and uninterrupted production process.
- Improved equipment lifespan: Preventive maintenance increases equipment lifespan by keeping the components in optimal condition and minimizing wear and tear.
- Cost savings: Proactive maintenance minimizes the need for costly repairs and emergency maintenance, reducing overall maintenance costs.
- Increased safety: Preventive maintenance ensures that the equipment operates safely and does not pose any risks to workers or the environment.
By incorporating a preventive maintenance program that suits your equipment and organizational goals, you can ensure optimal equipment reliability and efficiency, reducing unexpected downtime and costs.
Creating a Preventive Maintenance Program
Implementing a preventive maintenance plan is an essential step towards ensuring equipment reliability and prolonging its lifespan. Creating a well-defined preventive program involves several key steps that can be broken down into three phases: planning, implementation, and evaluation.
Phase 1: Planning
The planning phase involves setting up a preventive maintenance schedule and determining which components require regular maintenance. Creating a maintenance schedule helps ensure that these tasks are performed regularly and at the appropriate intervals to maximize equipment uptime and minimize downtime.
Tip: Consider using maintenance software to streamline the planning process and improve accuracy. This can help you stay on track with maintenance schedules and facilitate tracking tasks that are easy to overlook.
Phase 2: Implementation
During the implementation phase, it's time to put the complete guide to preventative maintenance to use. This involves carrying out regular inspections, general repairs and replacements, and performing scheduled maintenance tasks. By following the schedule and performing tasks on time, you can avoid costly breakdowns, optimize equipment performance, and keep operations running smoothly.
Tip: Create a maintenance checklist to ensure all tasks are correctly and consistently performed. This can help you stay on top of maintenance tasks and improve the reliability and longevity of equipment.
Phase 3: Evaluation
The final phase in the creation of a preventive maintenance system is evaluation. Evaluation helps you determine whether the maintenance program is effectively managing the equipment and making necessary adjustments to maintain equipment performance. It also helps identify pieces of equipment or parts that may need further enhancements or replacements to optimize reliability and efficiency in the PM program.
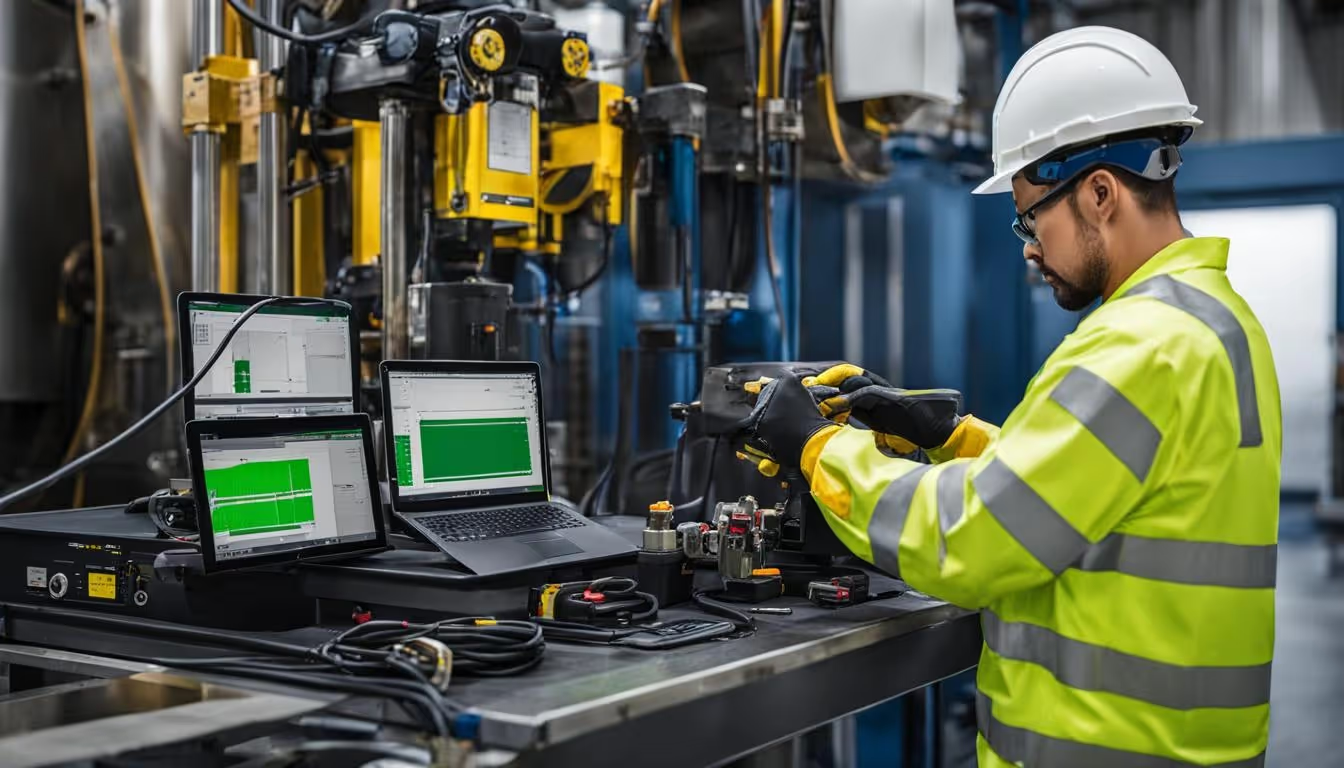
Creating a preventive maintenance program is crucial to ensuring equipment reliability and prolonging its lifespan. By implementing an effective program, you can minimize unexpected downtime, optimize equipment performance, and save money in the long run.
By using maintenance software, creating a maintenance schedule, and following it consistently, you will build a proactive maintenance program that delivers the reliability and efficiency you need to succeed.
Key Components of a Preventive Maintenance Procedure
Implementing a preventive maintenance program involves a meticulous approach that requires attention to details. In this section, we will discuss some essential components that are crucial to the effectiveness of your program.
Maintenance Procedures
Well-defined maintenance procedures are key to ensuring consistent performance and minimizing downtime. Failure to establish clear procedures can lead to confusion and errors, which can have adverse effects on equipment performance and reliability. Make sure to establish procedures that cover all aspects of maintenance for each piece of equipment, including inspections, cleaning, lubrication, and repairs.
Maintenance Checklist
A comprehensive maintenance checklist is a critical tool that guides technicians through the program. The list should include all tasks to be done, the tools and materials needed for each task, and the frequency of each task. The checklist should be visually accessible and easy to use, and it should be regularly updated to reflect changes in equipment and procedures.
"A good maintenance checklist is like a roadmap, providing a guide to preplanned equipment maintenance and helping to ensure excellent equipment performance and downtime reduction." Plant Manager
Equipment Maintenance
Regular equipment maintenance is a crucial component of preventive maintenance that involves taking good care of the equipment to ensure optimal performance and longevity. Maintenance tasks should include inspection, cleaning, lubrication, and repairs as necessary. You should also track the state of your equipment and provide any upgrades as needed to ensure you're utilizing it to its full potential.
By adhering to these key components, your preventive maintenance program will operate smoothly and effectively, ensuring your equipment is always running optimally.
Integrating predictive maintenance techniques
As we established in the previous section, preventive maintenance is a valuable tool for ensuring equipment reliability and minimizing downtime. However, predicting when maintenance is needed can be just as important as regular maintenance.
Predictive maintenance refers to the monitoring of equipment performance to detect signs of wear and tear before they become serious issues. By integrating predictive maintenance techniques into your preventive maintenance program, you can identify problems early and execute maintenance tasks before they become costly breakdowns.
Developing a maintenance plan and strategy that includes both preventive and predictive maintenance requires careful consideration and planning. It's crucial to define clear procedures and schedules for both types of maintenance activities. With the right maintenance software, you can automate and streamline the process, ensuring your equipment always receives the attention it needs.
Combining preventive and predictive maintenance can lead to significant cost savings by reducing overall equipment downtime, extending the lifespan of your assets, and minimizing repair costs. With a comprehensive maintenance plan in place, you can stay ahead of potential issues and ensure your equipment runs smoothly and efficiently for years to come.
Enhancing equipment reliability and efficiency
Regular maintenance procedures are essential for improving equipment reliability and efficiency. By scheduling routine maintenance checks and following established maintenance procedures, you can prevent equipment failure and extend the lifespan of your machines.
One of the key components of a successful preventive maintenance program is proactive measures. Identifying potential problems before they arise and taking steps to address them can save you time and money in the long run. Implementing a maintenance program can be a daunting task, but the benefits are clear.
“After implementing a comprehensive preventive maintenance program, our equipment downtime has significantly decreased, and our production output has increased. We are able to identify potential problems before they become serious issues, which has saved us time and money.” maintenance manager
In addition to regular maintenance procedures, using high-quality maintenance software can enhance the effectiveness of your maintenance program. With detailed maintenance schedules and automated reminders, these programs can help you keep track of all your maintenance tasks and ensure that nothing falls through the cracks.
To sum it up, a well-executed preventive maintenance program can protect your equipment, prolong its lifespan, and improve your productivity. By focusing on maintenance procedures, taking proactive measures, and utilizing maintenance software, you can enhance your company's equipment reliability and efficiency.
Conclusion
Implementing an effective maintenance program not only enhances equipment reliability and efficiency, but it can also prevent costly breakdowns.
By creating a maintenance schedule and utilizing maintenance software, you can stay on top of your equipment maintenance and avoid unexpected downtime. Remember to develop well-defined maintenance procedures, use a comprehensive maintenance checklist, and integrate predictive maintenance techniques for even better results.
Continuous improvement is key to achieving optimal equipment reliability and efficiency. By continuously refining your maintenance strategies, your preventive maintenance program will evolve and become more effective over time, saving you time and money in the long run.
With these best practices in mind, you are well-equipped to create and implement a preventive maintenance program that works for your organization and meets your unique needs. Start today and watch your equipment's reliability and efficiency soar!