AssetWatch AI Delivers Digital Transformation Across Division
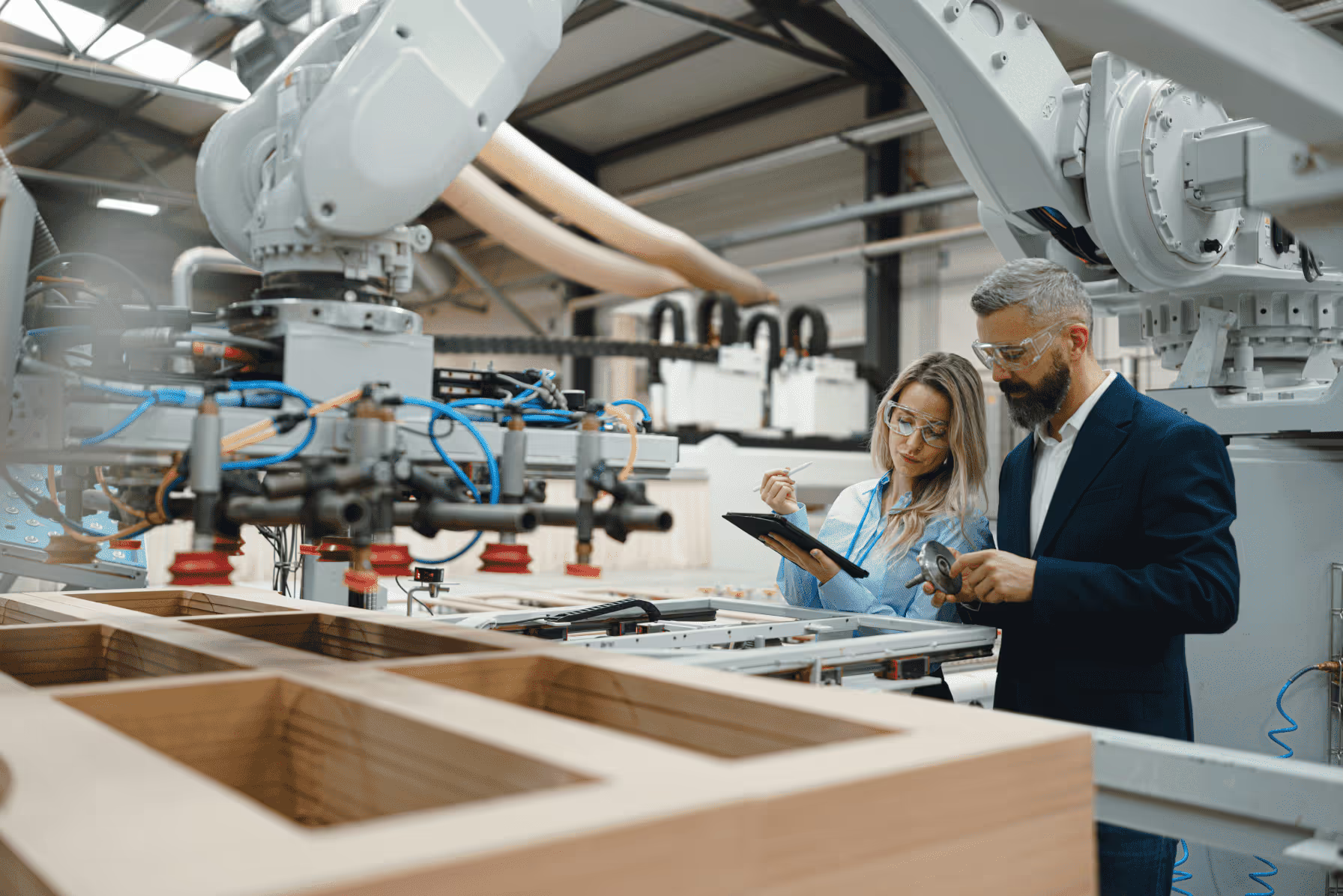
The Challenge
A leading North American producer of engineered wood products and plywood looked to capitalize on the growing availability of IoT and AI/machine learning tools to reduce unplanned equipment failures and improve productivity across all manufacturing facilities in their primary division. To help drive their plan for digital transformation, they wanted an industry 4.0 enterprise condition monitoring solution that would provide predictive maintenance insights, eliminate unplanned downtime on all rotating equipment, and be user-friendly for all stakeholders, including maintenance personnel, plant managers, reliability leaders, and C-suite executives.
The Journey
The customer evaluated several condition monitoring solutions and chose a six-month proof-of-concept (POC) with the AssetWatch end-to-end condition monitoring solution.
AssetWatch’s white-glove solution simplifies predictive maintenance by including all sensors and networking hardware, system installation and ongoing maintenance, cloud-based software, unlimited user licenses, and robust AI fault detection capabilities. A dedicated Condition Monitoring Engineer (CME) provides prescriptive maintenance recommendations as needed, helping avoid the alert fatigue common with comparable systems.
Rapidly deployable across the enterprise by AssetWatch’s team of expert field technicians, the combined vibration, temperature, and lubrication analysis solution is delivered as a SaaS model with simplified pricing based on the total number of sensors, requiring no upfront costs.
The customer’s Senior Innovation Engineer overseeing the project chose a critical manufacturing facility for the POC. AssetWatch’s technicians installed the complete system in less than two days, enabling AI to immediately begin analyzing data and delivering insights to AssetWatch’s dedicated CME.
During the six-month POC, AssetWatch’s powerful AI/CME combination delivered maintenance recommendations to the customer that allowed the customer to proactively address and resolve eleven machine faults before failure, documenting $113,000 in cost savings.
Seeing extraordinary results, the manufacturer subscribed at the POC facility and partnered with AssetWatch to develop a rollout plan to install the remaining fourteen divisional facilities over the next twelve months.
In addition to initial vibration/temperature condition monitoring, AssetWatch’s lubrication monitoring was added for oil-lubricated assets to gain comprehensive machine health insights on critical gearboxes, compressors and hydraulic systems, and CMMS integration was enabled.
The Results
Now fully deployed across all fifteen divisional facilities, the manufacturer has benefited from 130 resolved downtime risks, has received an ongoing 5x ROI, and has embraced AssetWatch as its AI-powered enterprise condition monitoring platform. In addition, plant managers, reliability leaders, and C-suite executives can now easily compare reliability performance metrics across facilities and institute best practices. Highlighting the shared success, the facility growth has mirrored the Senior Innovation Engineer’s rise to Senior Machine Learning Engineer, now overseeing machine learning and all digital innovation initiatives.
Sr. Division Reliability Engineer
$74k Boiler Pump Save
In one event that resulted in a $74k save for the customer, AI alerted to elevated vibration and non-synchronous harmonics on a boiler pump, indicating potential bearing failure. The AssetWatch CME analyzed the alert and issued a maintenance recommendation for the customer to grease the bearings and verify the bearing models. After receiving the information, the CME was able to isolate individual outer raceway defects on both pump bearings and issued a recommendation to swap the bearings at the next scheduled maintenance event. After replacing the bearings, vibration returned to normal levels and the customer provided an estimated $74k in cost savings from avoided downtime and maintenance hours.
How much could you save by using AssetWatch?
Get Started Today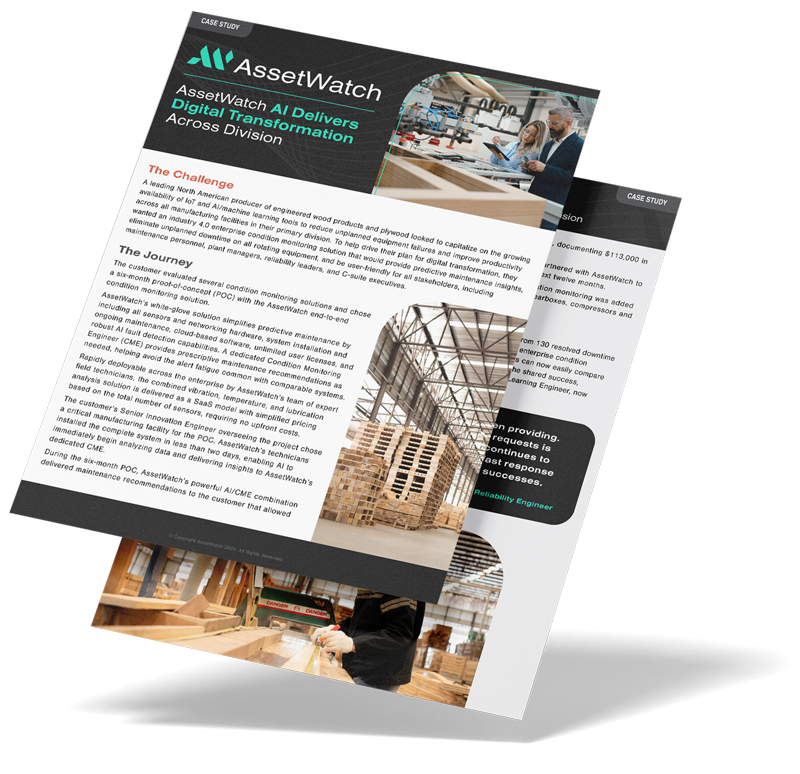
Find this case study helpful? We’d love to share it with you!
AssetWatch partnered with AWS to provide the scalability and reliability needed to support a serverless architecture. With a robust suite of services tailored for data ingestion, processing, and machine learning, AWS enables AssetWatch to seamlessly scale sensor data and deliver predictive insights to manufacturing companies. AWS infrastructure reduces operational overhead and allows AssetWatch to focus on innovation to drive value to our customers. Additionally, AWS’s strong security framework and global infrastructure ensure the resilience and compliance required to support mission-critical manufacturing operations at scale. This partnership positions AssetWatch to accelerate growth while maintaining the highest levels of performance and reliability.
.avif)

How much could you save by using AssetWatch?
Our 30-day, risk free trial is only $199.
AssetWatch customers save on average 8x in ROI. That means for every $1 you give us, we give $8 back to you.
Includes professional installation of up to 200 sensors (a $10k+ value)
24/7 monitoring and a dedicated CME for your site
AssetWatch cloud-based software with unlimited licenses
No CapEx, Engineering or IT integration required