Acoustic Analysis
Acoustic Analysis involves examining sound data to detect anomalies or changes in equipment operation. It's used in maintenance to identify issues like leaks, bearing failures, or misalignments without direct physical inspection, enabling early corrective actions to prevent further damage or failure.
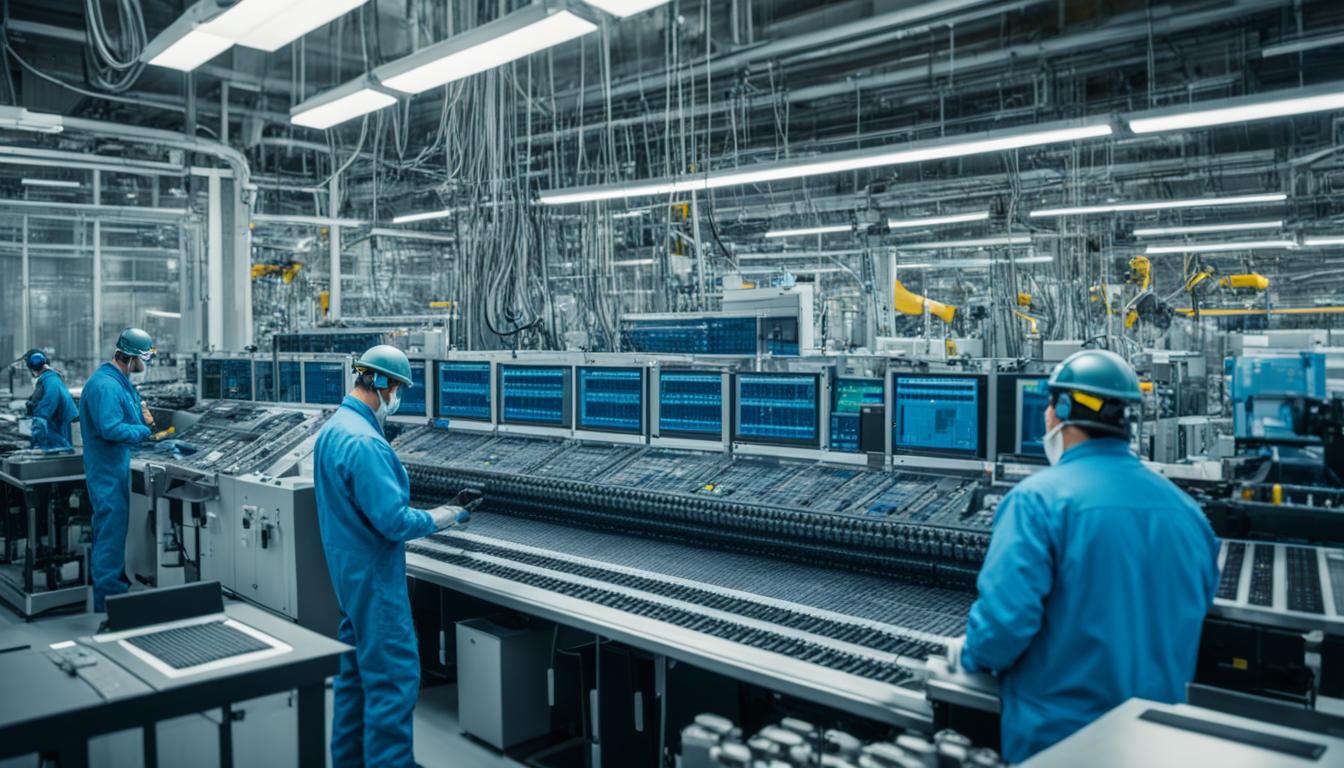
Acoustic Analysis in Manufacturing
In the fast-paced world of manufacturing, finding ways to boost efficiency and cut downtime is key. Acoustic analysis is a powerful tool for spotting machinery issues. It helps make your manufacturing process more efficient.
By using sound to measure and understand your equipment's condition, you can spot problems early. This leads to better predictive maintenance and monitoring.
This approach not only saves money but also improves how well your equipment works. It's a smart way to keep your manufacturing running smoothly.
Understanding Acoustic Analysis and Its Importance
Acoustic analysis is a key tool in manufacturing, especially for checking equipment condition. It uses sound waves to spot issues like wear, misalignment, and lubrication problems. Knowing these issues helps improve maintenance, moving from fixing problems after they happen to preventing them before they start.
Condition monitoring is very important. Using acoustic analysis helps find problems early. This leads to better maintenance and makes operations more efficient. Companies that use acoustic analysis often cut maintenance costs and make their equipment last longer.
- Enhanced detection of mechanical issues
- Improvement in maintenance planning
- Reduction in unplanned downtime
- Increased equipment longevity
Using acoustic analysis is part of smart predictive maintenance. It helps manufacturers predict and prevent failures. Making decisions based on sound signals keeps operations smooth and efficient.
Techniques and Technologies in Acoustic Analysis
Acoustic analysis uses different techniques and technologies to make manufacturing more efficient and reliable. It includes methods like vibration analysis and time-domain analysis. These help spot mechanical failures early, cutting down on downtime and maintenance costs.
Vibration analysis checks how machinery works by looking at vibrations with advanced sensors. It finds problems by watching for unusual vibrations. This helps keep machines running smoothly.
Smart acoustic sensors are changing the game by collecting important data for acoustic analysis. They let manufacturers check on their equipment in real-time. This means they can keep an eye on their machines all the time.
Adding machine learning to acoustic analysis makes interpreting data better. Many companies are investing in AI to improve data collection and analysis. This gives manufacturers clear advice on what maintenance to do next.
New tech in condition monitoring makes acoustic analysis even better. Now, you can use detailed data analysis tools for more accurate diagnostics. With these technologies, manufacturing processes get more efficient and safer.
Acoustic Analysis and Condition Monitoring
In today's fast-paced world, Acoustic Analysis is key in Condition Monitoring. It gives you vital insights into your machines' health. By using real-time sound data, you can check how well machines are doing and spot issues early. This helps you use Predictive Maintenance to keep your operations smooth and avoid big costs.
By always watching for unusual sounds, you can catch signs of trouble before it's too late. This lets you fix problems fast, keeping your machines running well and safely. The strength of Acoustic Analysis comes from combining it with other data like vibrations and temperatures. This creates a full Condition Monitoring system that boosts Manufacturing Efficiency.
Many companies have seen big gains from using acoustic analysis in their upkeep. Reports from groups like the American Society for Quality show how monitoring has greatly improved how things run and kept things safe. Using these new methods can make your equipment last longer and improve your production processes for better results.