Administration
Administration in the context of maintenance encompasses the organizational and managerial tasks required to support maintenance operations. This includes scheduling, budgeting, compliance management, and coordination of resources. Effective administration is crucial for ensuring that maintenance activities are carried out efficiently and align with organizational goals.
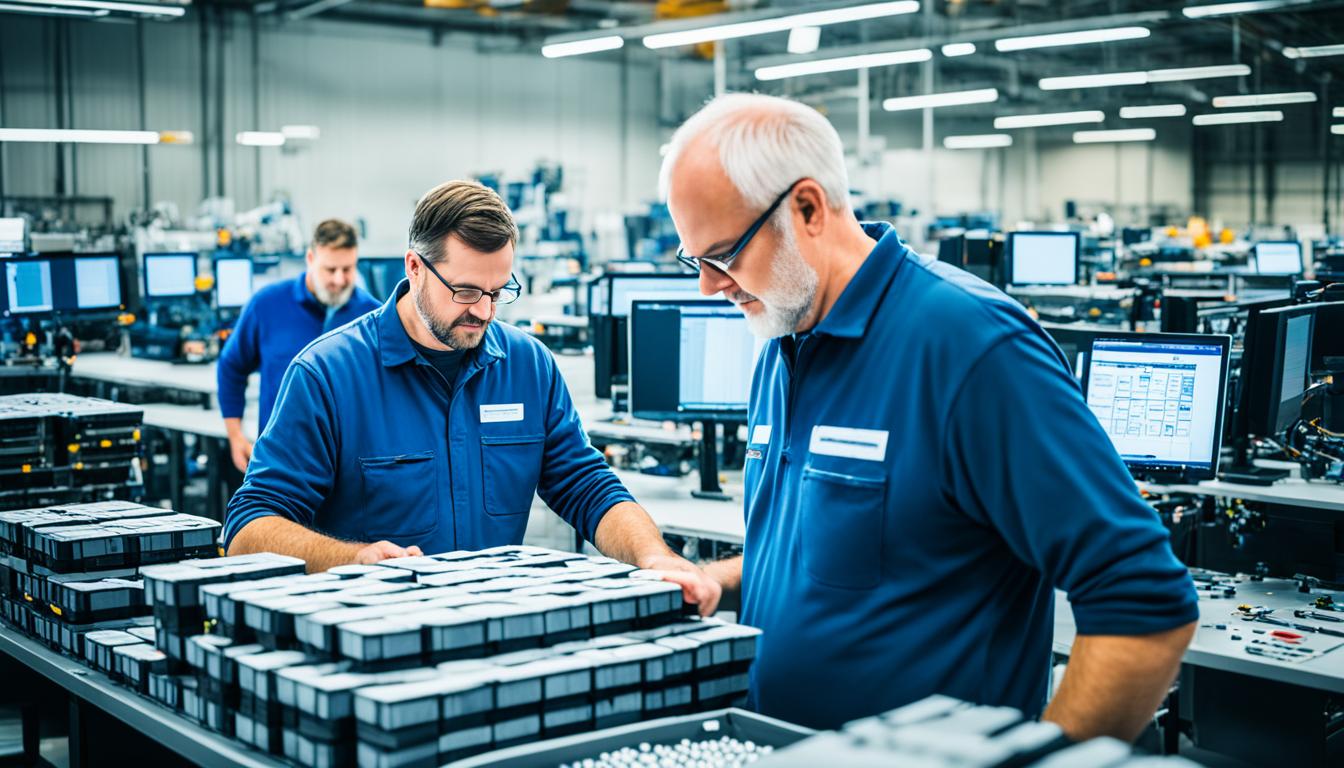
Administration in Manufacturing
In manufacturing, effective administration is key to doing well. It includes planning, organizing, directing, and controlling different parts of the operation. This is vital for using resources well, managing workflow, and making strategic decisions.
By focusing on good administration, you boost productivity and quality. This helps your business grow in a tough market.
Important roles like operations managers and quality assurance supervisors are crucial. They help make processes better and improve overall performance.
Understanding the Role of Administration in Manufacturing
Administration is key to making manufacturing successful. Skilled administrators make sure production runs smoothly and follows industry rules. They handle many important tasks to keep things running well and efficiently.
Some of the main tasks of administration include:
- Scheduling Production Runs: Getting the timing right boosts productivity.
- Maintaining Quality Control Systems: This keeps products trusted by clients.
- Managing Inventory Levels: It stops costs from getting too high or running out of stock.
- Coordinating Supply Chain Activities: This makes sure things get delivered on time and cuts down on delays.
Checking how things are doing is a big job for administrators. They look at data to make sure everything is working right. By always looking for ways to get better, they help make the company more efficient.
Linking good administration with managing operations makes a company more profitable and less wasteful. Being active in these areas helps a lot towards making manufacturing a success.
Administrative ResponsibilityImpact on ManufacturingScheduling Production RunsIncreases efficiency and reduces downtimeMaintaining Quality ControlEnhances product quality and customer satisfactionManaging InventoryMinimizes costs and prevents stockoutsCoordinating Supply ChainStreamlines delivery processes and reduces delays
Enhancing Efficiency Through Condition Monitoring
In today's competitive world, using advanced methods like Condition Monitoring boosts efficiency. It lets you check machinery performance in real-time. This way, you can spot problems early and avoid bigger issues, making operations smoother. This approach encourages your team to improve their work.
Vibration Analysis is a key part of Condition Monitoring. It looks at the vibrations from equipment. This helps find problems like misalignments or imbalances that slow things down. Regular checks give you the chance to fix problems fast, cutting down on unexpected stops.
These monitoring methods bring many benefits, including:
- Extended lifespan of machinery
- Significant cost savings on repairs
- Increased productivity and throughput
A recent study found a strong link between Condition Monitoring and better manufacturing results. Facilities that use these methods have fewer breakdowns and run more reliably. This proves that adding Condition Monitoring to your plan is key for lasting efficiency gains.
Benefits of Condition MonitoringImpact on OperationsProactive MaintenanceReduces unplanned downtimesCost SavingsLowers repair and replacement costsEnhanced ProductivityIncreases overall outputImproved Equipment PerformanceEnsures consistent operational levels
Using Condition Monitoring and Vibration Analysis in your strategy can greatly improve efficiency. It helps make your manufacturing more reliable and resilient.
Integrating Predictive Maintenance into Your Administration Strategy
In today's manufacturing world, staying ahead means being proactive with equipment maintenance. Adding predictive maintenance to your strategy is key. This method uses advanced analytics to predict equipment failures before they occur. This lets you fix problems early, cutting downtime and boosting productivity.
Predictive maintenance and prescriptive insights help you make smart maintenance plans and budgets. By tracking key performance indicators (KPIs), you set clear goals for maintenance. Training your team helps them use these new strategies well. A focus on continuous improvement motivates staff to find better ways to work, making things more efficient.
Many companies have seen big wins with predictive maintenance. For example, a top car maker cut down on unexpected downtime with predictive analytics. By using these new maintenance methods, you can build a strong operation. This prepares you for surprises and helps you grow in a changing market.