Analysis
Analysis in maintenance refers to the systematic examination of data, processes, or systems to identify issues, determine causes, and develop solutions. It can include failure analysis, root cause analysis, and performance analysis, providing insights that guide maintenance decisions and improve reliability and efficiency.
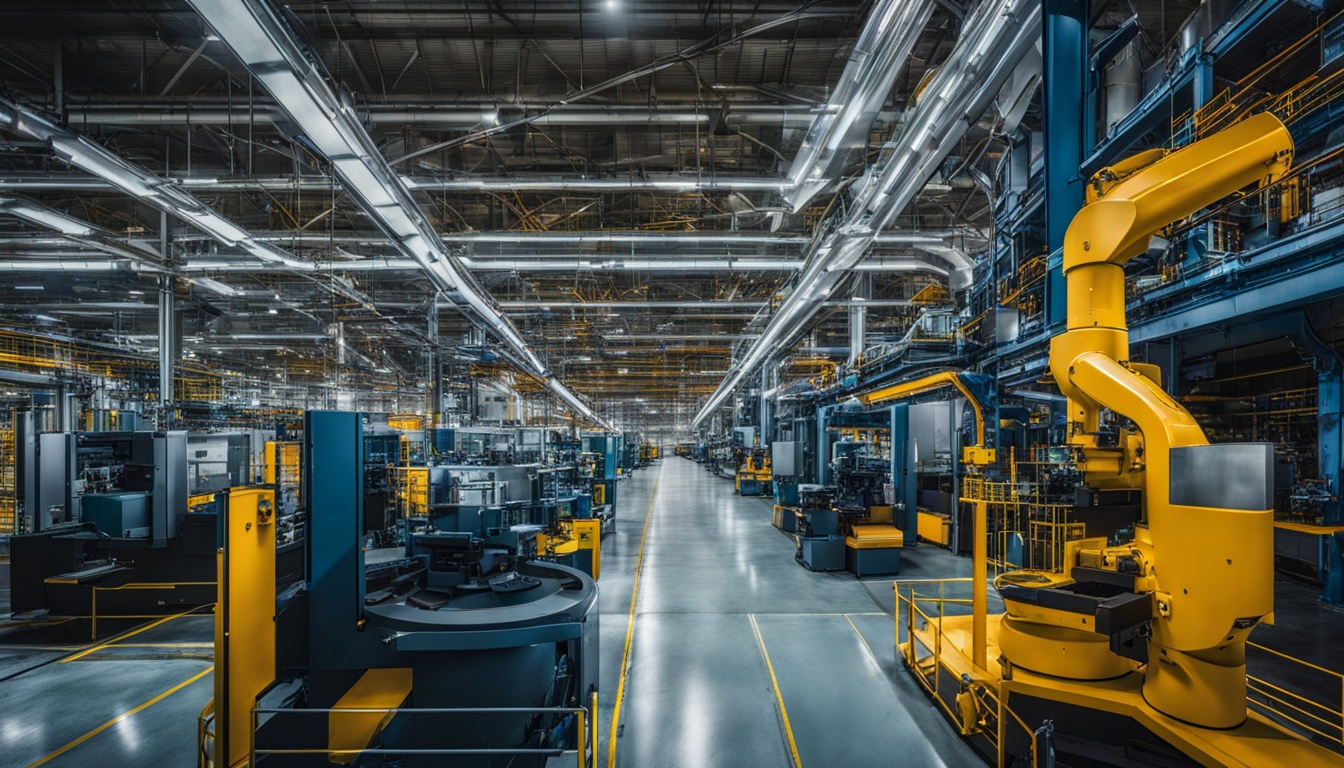
Analysis in Manufacturing
In today's fast-paced world, analysis is key in manufacturing. Using accurate data and performance metrics boosts efficiency. It helps you make smart, data-driven choices that drive innovation.
When companies use analytical tools well, they spot patterns and trends. This leads to better productivity and lower costs. For example, data visualization tools turn complex data into clear insights. This helps your operations flow better.
Analysis also helps improve production and supports ongoing improvement. It keeps you ahead in the market. By using analysis, you can make your business more efficient and competitive.
The Importance of Analysis in Manufacturing
Analysis is key in manufacturing. Using data analysis and condition monitoring boosts productivity a lot. It helps spot areas to improve, making production more efficient.
Looking at operational data helps find bottlenecks that slow down production. Fixing these problems early makes the operation smoother and faster. Also, analyzing data lets manufacturers check how well equipment is working. This helps make maintenance decisions on time, reducing downtime.
With Industry 4.0, real-time analysis is more important than ever. Making decisions based on data lets you quickly adjust to changes and improve processes. Focusing on analysis improves equipment and overall performance, leading to better operations.
Techniques for Effective Analysis
To get the most out of your manufacturing, using data analysis techniques is key. Vibration analysis is a top method that keeps an eye on machinery health. It tracks vibration to spot potential failures early, avoiding expensive downtime. This helps with predictive maintenance, keeping your equipment running well.
Adding vibration analysis to your maintenance plan brings big benefits:
- Identifying wear and tear in components
- Forecasting machine failures
- Facilitating timely interventions
Also, using statistical process control (SPC) and root cause analysis (RCA) can improve your manufacturing. These methods help find defects and make processes better. By combining these, you'll make your products better and your operations more efficient.
Implementing Predictive and Prescriptive Maintenance
In today's competitive world, using predictive maintenance is key for reliable equipment and less downtime. By analyzing advanced data, you can spot when equipment might fail. This lets you fix things before they break, keeping your production smooth.
Prescriptive maintenance takes it up a notch by giving advice on how to fix issues. It combines predictive analysis with actionable tips to improve maintenance plans. This way, you can make your maintenance more effective, extend your equipment's life, and save money.
Going proactive with maintenance can boost your product quality and profits. Using predictive and prescriptive maintenance helps you make your manufacturing process stronger. This keeps you competitive and ensures your equipment works well.
Our 30-day, risk free trial is only $199.
AssetWatch customers save on average 8x in ROI. That means for every $1 you give us, we give $8 back to you.
Includes professional installation of up to 200 sensors (a $10k+ value)
24/7 monitoring and a dedicated CME for your site
AssetWatch cloud-based software with unlimited licenses
No CapEx, Engineering or IT integration required