Area Maintenance
Area Maintenance refers to the practice of assigning maintenance responsibilities based on specific geographic areas or locations within a facility. It ensures that all parts of the facility receive regular maintenance attention, improving overall operational reliability and safety.
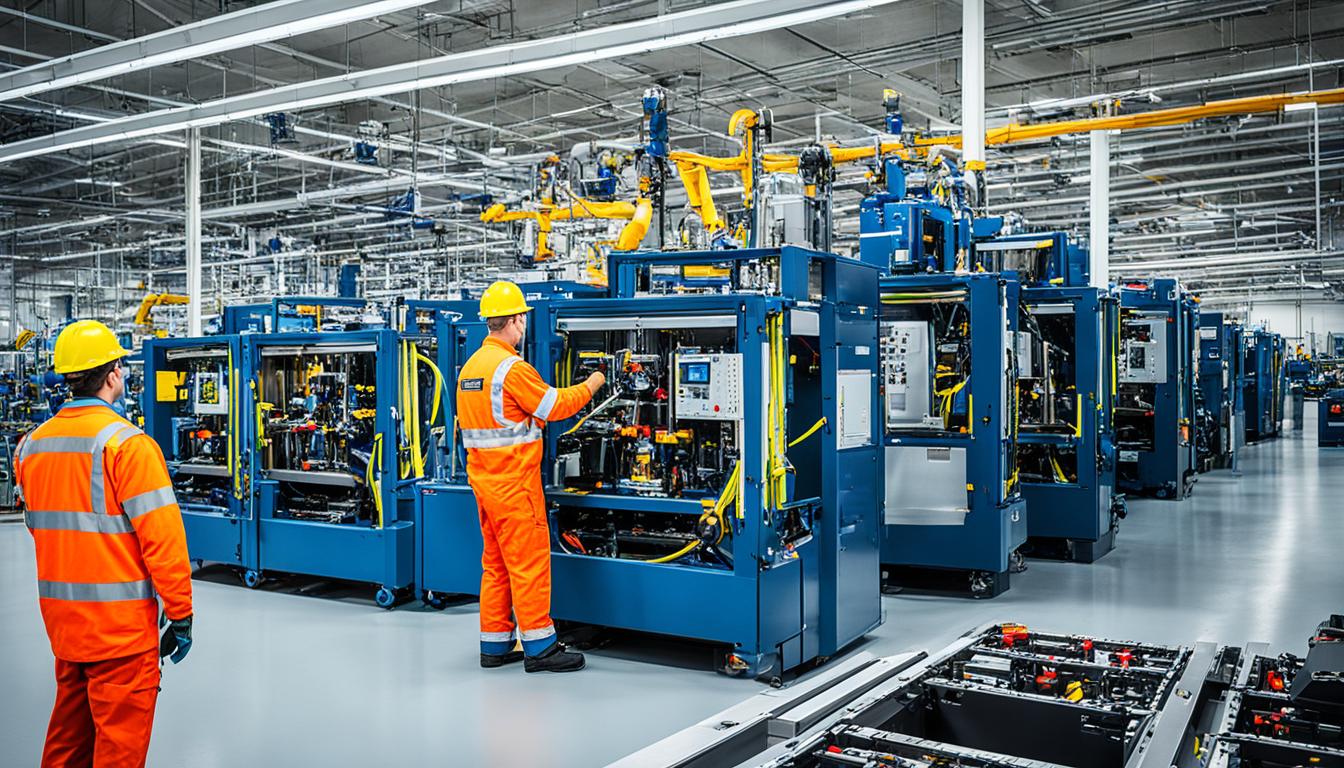
Area Maintenance in Manufacturing
In the fast-paced world of manufacturing, keeping the workspace and equipment in top shape is key. Area maintenance means doing the right things to make sure your machines work well. By sticking to regular maintenance and using smart system care, you can make your manufacturing process more efficient.
Keeping an eye on your equipment's condition is also crucial. This lets you spot problems early, cutting down on downtime and saving money on repairs. As you learn more about area maintenance, you'll see how it helps make your manufacturing process reliable and productive.
Understanding Area Maintenance and Its Importance in Manufacturing
Learning about area maintenance is key to making manufacturing systems better. It boosts productivity and makes equipment last longer. With a good plan, you can work more efficiently and cut down on downtime.
Area maintenance includes important parts like preventative maintenance and condition monitoring. These help keep all equipment running well. Preventative maintenance does regular tasks to stop problems before they start. This way, you avoid sudden breakdowns and make your manufacturing more reliable.
Condition monitoring works with preventative maintenance by giving real-time updates on equipment status. This lets you fix issues early, preventing bigger problems. By watching your machines closely, you can lower the risk of unexpected failures.
Let's look at the main parts of area maintenance and their benefits in this table:
Using a strong area maintenance strategy is crucial for your manufacturing systems. It helps cut costs and boost productivity. Understanding these parts lets you make better choices, leading to ongoing success in your operations.
Integrating Condition Monitoring into Area Maintenance
Adding condition monitoring to area maintenance changes how you handle equipment and operations. It uses real-time data for making proactive decisions in your manufacturing process.
Techniques like vibration analysis let you check equipment health all the time. This helps spot problems early, avoiding expensive downtime and maintenance issues.
- Increased equipment uptime through timely interventions
- Data-driven analysis to aid in predictive maintenance
- Enhanced safety standards by reducing unexpected failures
Using condition monitoring tools gives you important insights for your maintenance plans. These tools offer detailed advice on when and how to do maintenance, keeping equipment running well.
With condition monitoring, your area maintenance gets a big boost. Predictive maintenance and actionable insights improve your manufacturing's efficiency and reliability.
Area Maintenance Strategies: From Preventative to Predictive
In the manufacturing world, Area Maintenance Strategies are key to keeping things running well. Before, companies used Preventative Maintenance to keep their equipment in good shape. This method includes regular checks and fixes to avoid sudden breakdowns. But, it can sometimes mean doing more maintenance than needed, wasting time and resources.
Now, with new technology, companies are moving to Predictive Maintenance. This method uses real-time data to watch over equipment conditions. It helps spot problems before they start, cutting down on downtime and costs. By using data analytics, companies can plan their maintenance better, fixing things only when it's really needed.
Maintenance Optimization combines the best of both worlds. It uses Preventative and Predictive Maintenance together to meet specific needs. This way, companies can make their equipment last longer, follow safety rules, and meet industry standards better.
The Future of Area Maintenance: Leveraging Technology
The world of area maintenance in manufacturing is changing fast, thanks to new technology. Automation and connectivity are making big changes on the manufacturing floor. You might need to update your maintenance plans to keep up.
With the rise of the Internet of Things (IoT), expect more real-time data and condition monitoring. This tech gives you detailed info on how equipment is doing. It also lets you plan maintenance before problems get worse.
Artificial intelligence and machine learning will also change how you maintain things. They help automate tasks, use resources better, and make decisions based on past data. By using these new technologies, area maintenance will become more efficient and connected.