Assessment Reliability
Assessment Reliability involves evaluating the dependability and consistency of maintenance assessment processes and tools. It ensures that maintenance evaluations accurately reflect equipment condition and maintenance needs, supporting effective decision-making and planning.
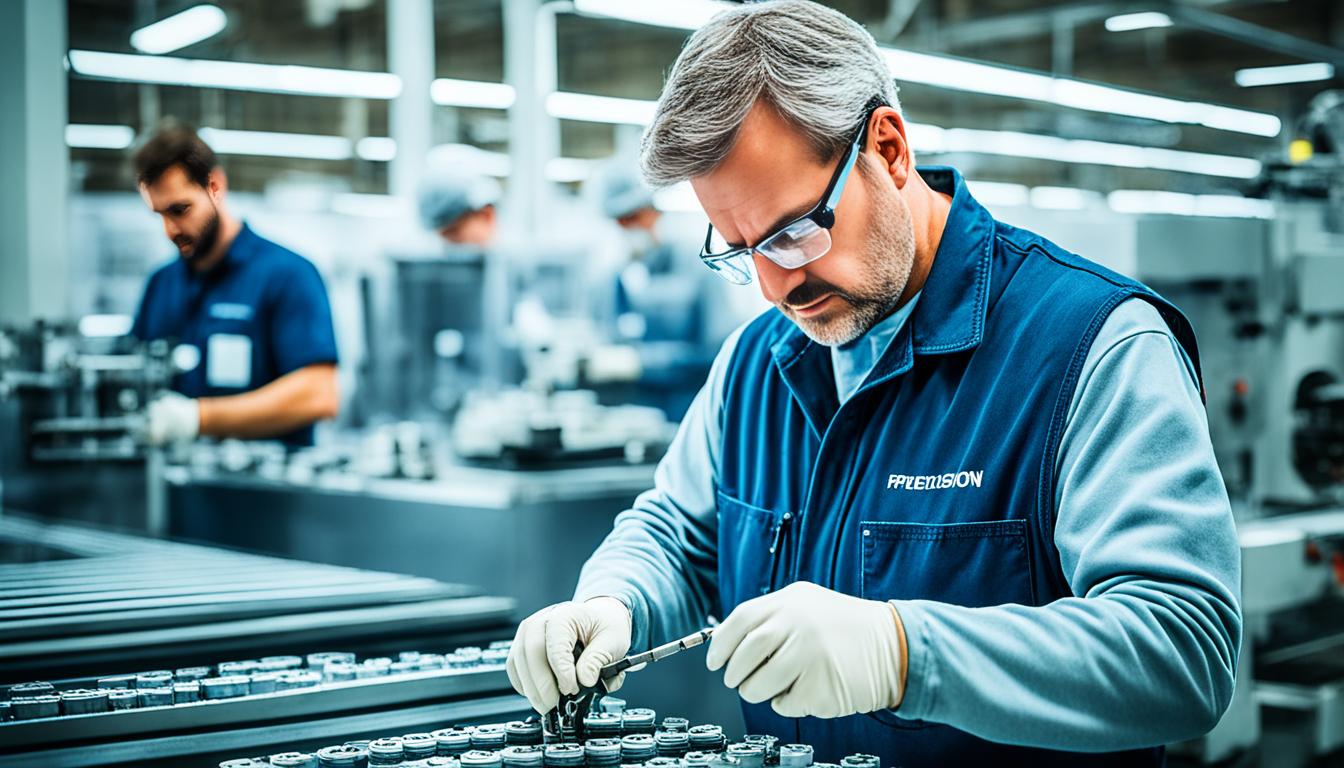
Assessment Reliability in Manufacturing
In the fast-paced world of manufacturing, Assessment Reliability is key. It helps you make smart decisions and protect your investment. It means checking how well your equipment works and its condition often. This way, you can avoid sudden stoppages and cut costs.
Experts like the National Institute of Standards and Technology (NIST) say a good assessment process is vital. It boosts your system's performance and keeps you competitive.
Tools like Condition Monitoring and Vibration Analysis are crucial for keeping things reliable. They let you spot problems early. This means you can fix them before they cause big issues, keeping your operations running smoothly.
Understanding Assessment Reliability in Manufacturing
Knowing how to make assessments reliable in manufacturing is key to better maintenance. It's a big part of your maintenance plan, helping you use predictive maintenance well. By focusing on assessment reliability, you can spot and fix equipment problems before they get worse.
Using reliable ways to assess helps you move from fixing problems after they happen to preventing them. This saves money and makes your production better. Tools like vibration analysis and condition monitoring are key for reliable assessments. They make your operations safer and help your equipment last longer.
- Promotes early detection of potential failures
- Increases equipment reliability and lifespan
- Enables cost-effective solutions through predictive maintenance
- Reduces operational disruptions, enhancing efficiency
By focusing on these methods, companies can change their maintenance plans for the better. They meet industry standards and work towards being the best they can be.
Methods for Ensuring Assessment Reliability
Ensuring assessment reliability in manufacturing is key for top performance. Different techniques make the evaluation process better and help operations work well. Prescriptive Maintenance is a big help, giving clear advice based on data from assessments. It warns you about possible equipment failures and tells you how to stop them.
Condition Monitoring is also crucial. It keeps an eye on machine performance all the time, making sure assessments are reliable. This way, you get real-time data that helps you make smart choices to improve manufacturing.
Using new tech like IoT and machine learning takes these methods to the next level. These technologies make data more accurate, leading to better assessments and keeping high standards of reliability. Experts say using these new strategies can really boost reliability and efficiency in making things.
Impact of Assessment Reliability on Maintenance Strategies
Assessment Reliability is key to making maintenance plans better. It lets you use Predictive Maintenance, which means fixing things when they need it, not just on a schedule. This makes your operations run smoother and keeps your machines working well.
Using Assessment Reliability means you don't just follow a one-size-fits-all maintenance plan. This can lead to wasting time or spending too much money. Predictive Maintenance uses data to plan maintenance better, cutting down on downtime and unexpected equipment failures.
Also, reliable assessments help you make smart choices about where to use your resources. You can focus on the most important maintenance tasks. This way, you keep improving and getting better at what you do, which is key for doing well in manufacturing.
Companies that use Assessment Reliability see big improvements in how they work. They have healthier equipment and spend less on maintenance. Moving to reliable assessments, especially with Predictive Maintenance, makes your maintenance plans much better.
Challenges in Achieving Assessment Reliability
Getting reliable assessments in manufacturing is key but tough. Many companies struggle with the high cost of advanced condition monitoring systems. These systems are vital but can be expensive, especially for small businesses. This can stop them from setting up a strong reliability strategy.
Another big challenge is finding skilled people. You need experts to understand and interpret the data from these systems. Without them, you might miss important signs, leading to bad decisions and more problems later.
Also, adding new tech to old systems can be tricky. Moving to data-driven maintenance is complex, especially when trying to make different systems work together smoothly. The Engineering Maintenance Systems Association says that many manufacturers face too much data, making quick decisions hard. To beat these issues, it's important to invest in training and update your tech. This will help your company use assessment reliability to its fullest.