Asset Condition Monitoring
Asset Condition Monitoring is the practice of continuously monitoring and analyzing the condition of assets to detect signs of wear, failure, or degradation. It uses various diagnostic tools and technologies, such as vibration analysis, thermal imaging, and acoustic monitoring, to provide real-time insights into asset health. This proactive monitoring helps in scheduling maintenance activities strategically to prevent unplanned downtime and extend asset life.
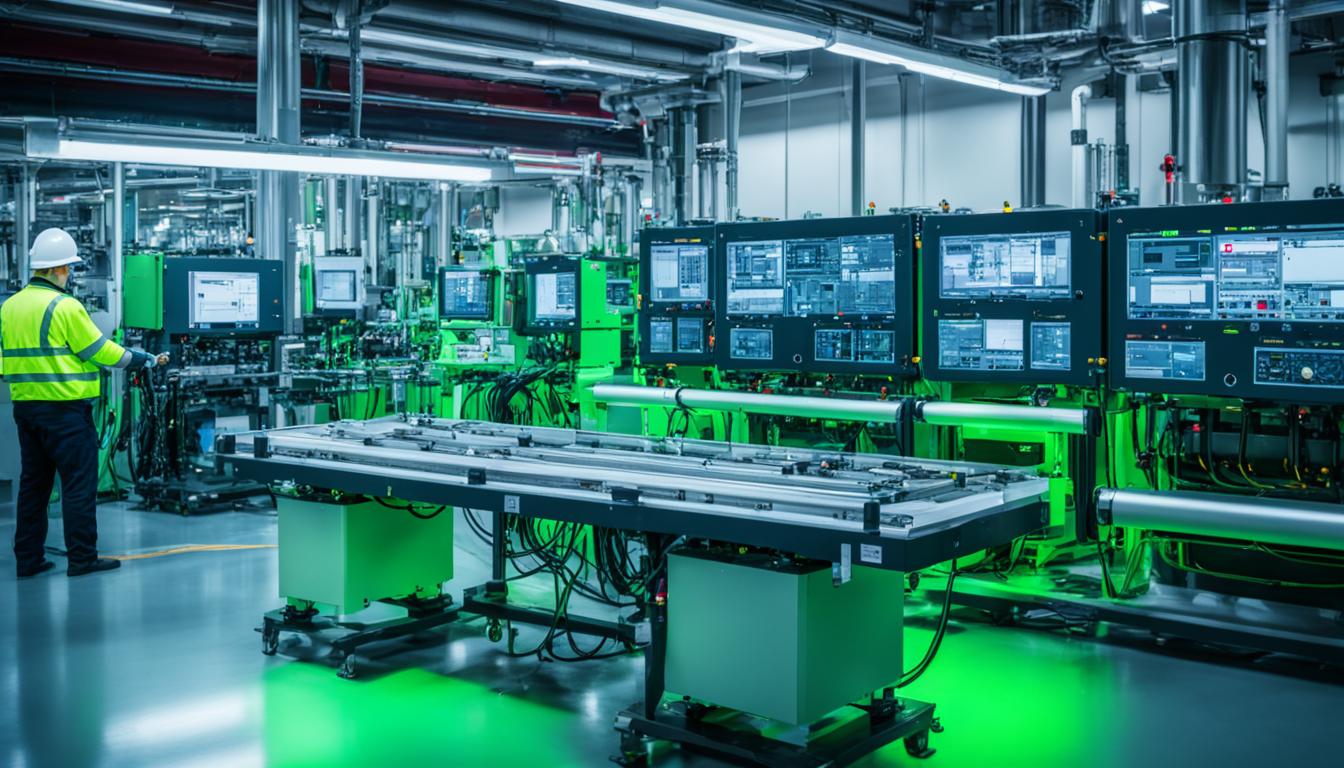
Asset Condition Monitoring in Manufacturing
In today's fast-paced manufacturing world, Asset Condition Monitoring (ACM) is key to boosting Manufacturing Efficiency. This approach lets you check on your equipment's health. It ensures your Equipment Reliability goes up and cuts down on sudden breakdowns.
Using predictive and preventative maintenance, you can fix your machines only when needed, not just on a set schedule. With ACM, tools like vibration analysis, thermal imaging, and ultrasonic testing give you important data. This data helps make your operations smoother, raising productivity.
Understanding Asset Condition Monitoring
Asset Condition Monitoring is key to making manufacturing equipment more reliable. It uses real-time checks to make sure equipment works well and cuts down on unexpected downtime.
Key parts of Asset Condition Monitoring include:
- Vibration Analysis: This method spots mechanical problems early. By watching for vibrations, you can catch issues like misalignments before they get worse. This helps avoid big failures.
- Temperature Monitoring: Watching the heat levels tells you if parts might overheat. Catching this early lets you fix problems before they cause damage.
- Oil Analysis: Checking the oil condition of machinery shows how well parts are wearing. The right oil condition is crucial for good equipment performance.
These parts work together to send important data to operators. This data helps make maintenance plans that fit your specific needs. Predictive maintenance is a big part of this. It uses data to predict when equipment might break down. This way, you can plan maintenance ahead, use resources better, and make your equipment last longer.
Benefits of Asset Condition Monitoring
Asset Condition Monitoring is key to better manufacturing processes. It makes your equipment more reliable. By using real-time data, you can spot maintenance issues early and avoid big problems.
Adding Asset Condition Monitoring to your operations boosts efficiency. It helps you keep track of your equipment's condition. This means less unexpected downtime and a smoother workflow. Regular checks and analysis help you keep getting better.
Getting prescriptive insights from your ACM system changes how you maintain things. You'll know when maintenance is needed and the best way to do it. This helps extend the life of your assets and improve how well they work.
There are big financial benefits too. A good Asset Condition Monitoring program saves money by planning maintenance better and cutting down on emergencies. This leads to more work getting done and higher profits.
Implementing Asset Condition Monitoring in Your Manufacturing Process
Adding Asset Condition Monitoring to your manufacturing process is key to boosting efficiency and cutting downtime. Start by picking out the most critical assets to watch. This helps you focus on the equipment that could most disrupt your work.
Then, choose the best condition monitoring methods for your gear. Options like vibration analysis and thermal imaging work well for different types of assets. With the right tools and software, you can gather data easily and make smart, proactive choices. It's also crucial to train your team to understand the data, as their skills will affect your maintenance success.
Finally, keep refining your monitoring approach based on the data you gather. Regularly check how well your monitoring methods work and be ready to adjust them as needed. This ensures your monitoring stays in step with your manufacturing needs, leading to better performance over time.