Asset Optimization
Asset Optimization in maintenance involves strategically maximizing the value and performance of an organization’s assets while minimizing costs and risks. It focuses on improving asset availability, reducing maintenance expenses, and enhancing overall equipment effectiveness (OEE) and remaining useful life (RUL) of assets. By optimizing asset utilization, businesses can achieve better operational efficiency and financial outcomes.
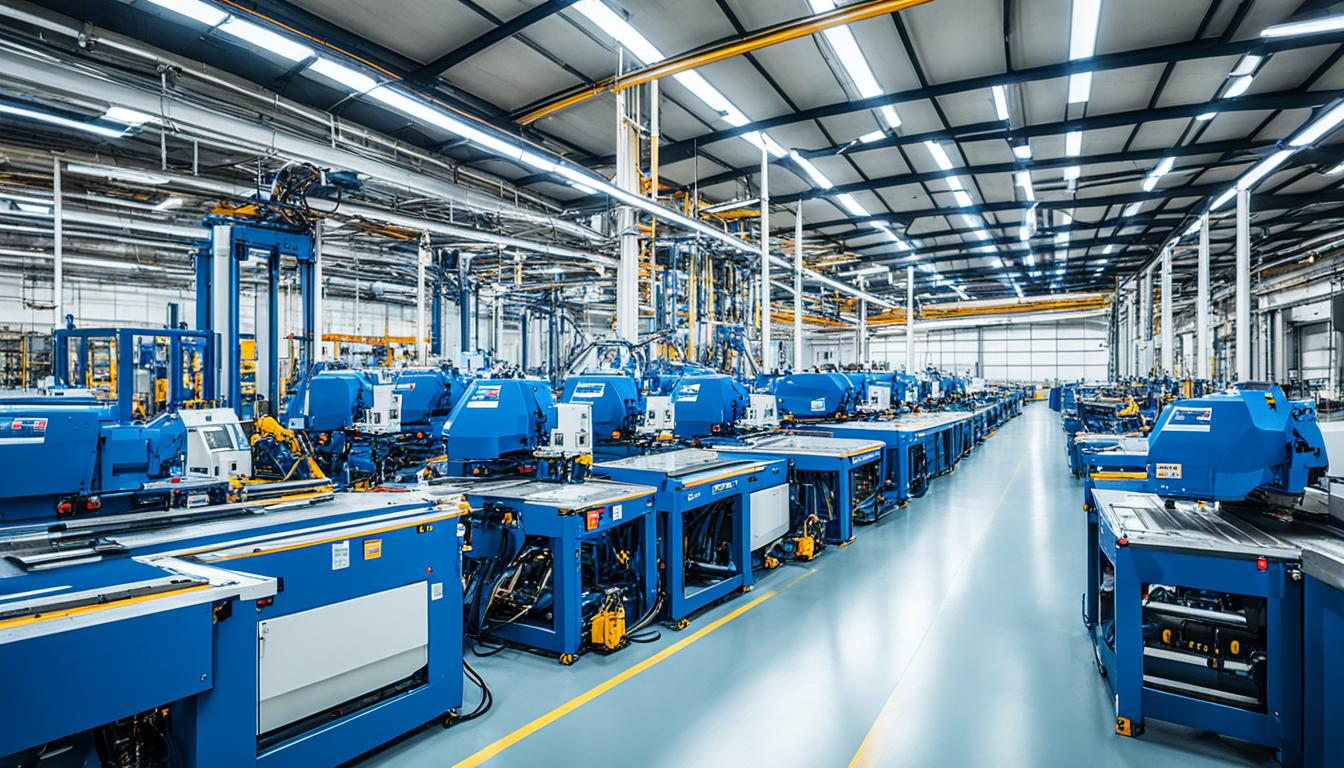
Asset Optimization in Manufacturing
Asset optimization is key to making manufacturing more efficient. By managing your assets like machinery well, you can make production better and cut down on downtime. This approach not only boosts performance but also saves your company money.
According to a Deloitte report, companies that use smart asset optimization can reduce downtime by up to 30%. It's vital for any manufacturing business that wants to use its assets fully.
Understanding Asset Optimization in Manufacturing
Understanding Asset Optimization is key to better manufacturing processes. It's about using your assets well and keeping operations smooth. Using smart Asset Management Strategies can greatly improve how well and efficiently things work.
Asset Optimization brings many benefits. It makes assets more reliable, so they break down less often. This leads to a smoother workflow. Companies that use these strategies often see lower maintenance costs. They avoid big problems by acting early.
Studies show that focusing on asset optimization can increase asset availability by 10-15%. This shows how well these methods work.
To make asset optimization work, focus on preventive maintenance. Regular checks and services can stop problems before they start. Using new tech like IoT and artificial intelligence helps too. These tools let you monitor assets in real-time and understand how they're doing.
By understanding and using Asset Optimization, your company can keep moving forward and stay competitive. These strategies help you manage and use your resources well. You'll see real benefits from them.
Implementing Condition Monitoring Techniques
Condition monitoring is key to keeping your manufacturing assets running well for a long time. It checks the health of your machines and gear. This way, you can avoid expensive downtime and boost how well things work.
Using methods like vibration analysis, thermography, and ultrasonic testing gives you real-time data. This helps you understand how your assets are doing.
These methods offer important insights. They let you spot problems early, before they get worse. For example, vibration analysis can find if a machine is out of balance. Thermography can spot if something is getting too hot.
Using these techniques leads to a smarter maintenance plan.
- Vibration Analysis: Monitors changes in machine vibrations for early fault detection.
- Thermography: Uses thermal imaging to pinpoint overheating and insulation problems.
- Ultrasonic Testing: Detects high-frequency sounds produced by machinery, indicating issues.
Companies that use these monitoring techniques often see big gains in their assets' performance. They last longer. This proactive maintenance approach makes maintenance more efficient. It also prepares your assets for the future.
Asset Optimization: Predictive and Prescriptive Maintenance
Using predictive and prescriptive maintenance can greatly improve how you manage your assets. Predictive Maintenance uses advanced data analytics to forecast when equipment might fail. This lets you plan maintenance before problems happen, avoiding sudden breakdowns. Prescriptive Maintenance takes it further by giving you specific advice based on your operations.
Studies show that companies using predictive maintenance can cut maintenance costs by 10% to 40%. By adopting these new methods, you can improve performance and match your maintenance plans with your production goals better.
- Predictive Maintenance: Cuts unplanned downtime and makes assets last longer.
- Prescriptive Maintenance: Gives advice to make maintenance more efficient.
By using both predictive and prescriptive maintenance, you can change your maintenance plans. This will help you use your manufacturing assets more efficiently.
Leveraging Vibration Analysis for Asset Performance
Vibration analysis is key in optimizing asset performance. It lets you check the vibrations of your machinery to spot issues like misalignment or mechanical faults. This helps keep your assets running smoothly.
This method is great because it doesn't need to stop your machines to work. It helps find problems early, cutting down on maintenance time and costs. Studies show that using vibration analysis can save up to 40% on maintenance and make assets more reliable.
It also makes the workplace safer. By catching mechanical problems early, you avoid sudden equipment failures that could harm your team. Investing in vibration analysis protects your assets and keeps your team safe, making your operations more productive and sustainable.