Big Data
Big Data refers to extremely large data sets that may be analyzed computationally to reveal patterns, trends, and associations, especially relating to human behavior and interactions. In manufacturing, big data analytics help in optimizing production processes, predictive maintenance, and enhancing product quality by analyzing vast amounts of operational data.
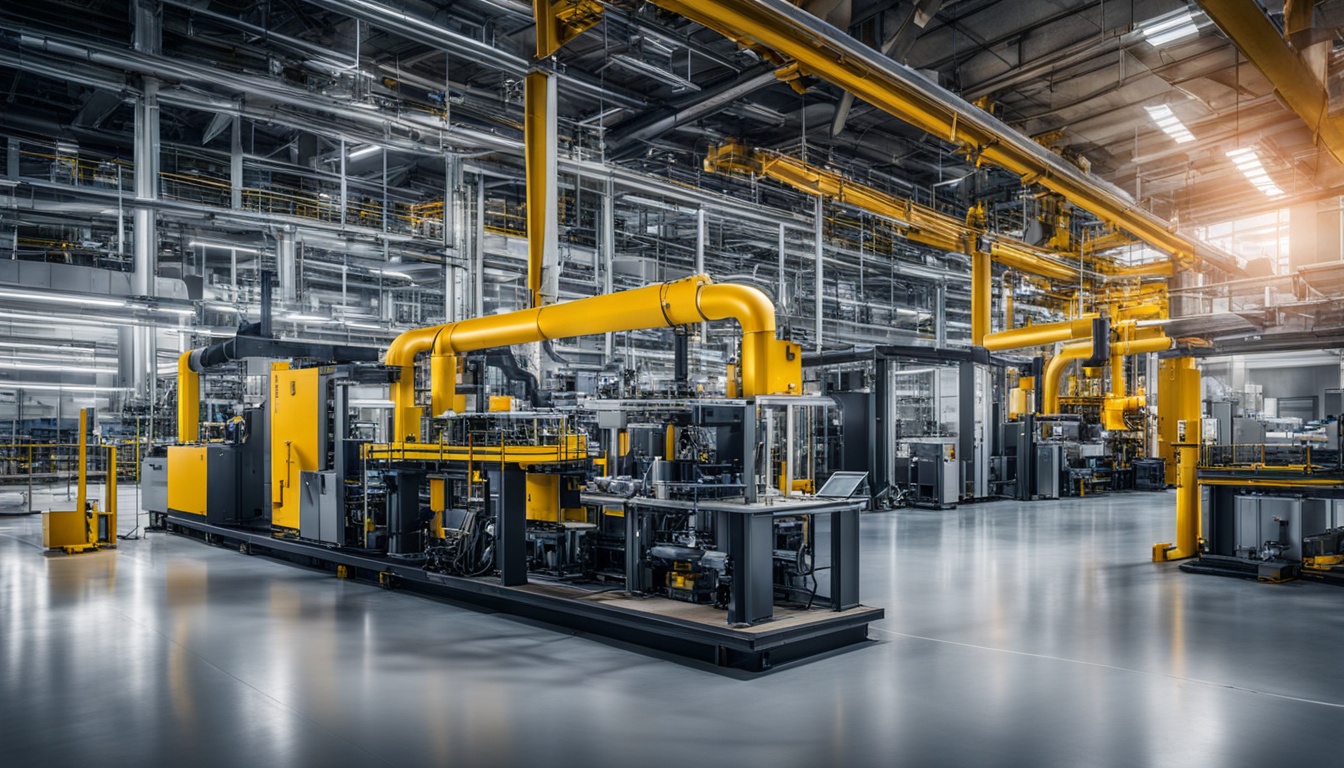
Big Data in Manufacturing
In the fast-paced world of manufacturing, Big Data has changed how we run our businesses. It's the huge amount of structured and unstructured data from production. This data offers big chances for better efficiency and deeper insights. By using this data, you can make your operations smoother, push innovation, and stay ahead in the market.
Companies like GE and Siemens are leading the way in using Big Data analytics. They're changing their manufacturing for the better. Think about how Big Data can make your decisions better, improve product quality, and cut production costs. Big Data brings real-time analysis and better supply chain management, making a big difference in manufacturing.
The Role of Big Data in Modern Manufacturing
Big Data has changed how Modern Manufacturing works. It helps make things more efficient and smooth. By using data to make decisions, manufacturers can find ways to get better and cut down on downtime.
Companies that use Big Data see big wins. A stud done found that using Big Data can make operations up to 20% better. With the right analytics, you can spot where things are slow, helping you use resources better.
Having real-time data is a big plus of Big Data. You can quickly fix problems and keep up with quality issues. This quick action is key in today’s fast-moving manufacturing world. In short, using Big Data helps make your operations better and encourages making decisions based on data.
Leveraging Big Data for Predictive and Prescriptive Maintenance
In the manufacturing world, Big Data changes how companies handle maintenance. It uses predictive and prescriptive strategies. Predictive Maintenance uses advanced analytics to guess when equipment might break down. This lets you fix problems before they happen.
This proactive approach cuts down on unexpected downtime and boosts efficiency. Studies show that predictive maintenance can save 10% to 40% on maintenance costs. These savings come from better planning and fewer emergency repairs.
As data from sensors and equipment flows in, you get insights that guide your maintenance plans. This leads to smarter maintenance schedules and better use of resources.
Prescriptive Maintenance goes beyond just predicting failures. It also suggests what actions to take. With Big Data insights, you can plan maintenance better and use resources wisely. This means your equipment lasts longer and production stays smooth.
Using Big Data clearly shows its value in cutting maintenance costs and boosting performance. Understanding these ideas helps you make smart choices for your manufacturing future.
Condition Monitoring and Vibration Analysis in Manufacturing
Condition monitoring is key to keeping manufacturing equipment running long and well. It checks the health of machinery all the time, using different methods. Vibration analysis is a big part of this, using Big Data to spot problems before they start.
Advanced sensors and the Internet of Things (IoT) play a big role in this. They help capture and understand vibration data. This lets you keep an eye on your equipment's condition all the time. Companies that use this can see up to a 25% drop in equipment failures.
Adding condition monitoring to your manufacturing means you're looking ahead for equipment care. By focusing on vibration analysis, you can make a strong maintenance plan. This plan cuts down on downtime and boosts productivity. Using Big Data in condition monitoring also makes your workplace safer and more reliable.