Capacity Utilization
Capacity Utilization measures the extent to which an organization uses its installed productive capacity. It is a percentage indicating how much of the total manufacturing output capacity is being utilized at a given time. High capacity utilization indicates efficient use of resources, while low utilization can signal inefficiencies or excess capacity. In maintenance, ensuring equipment is available and reliable is key to maintaining high-capacity utilization.
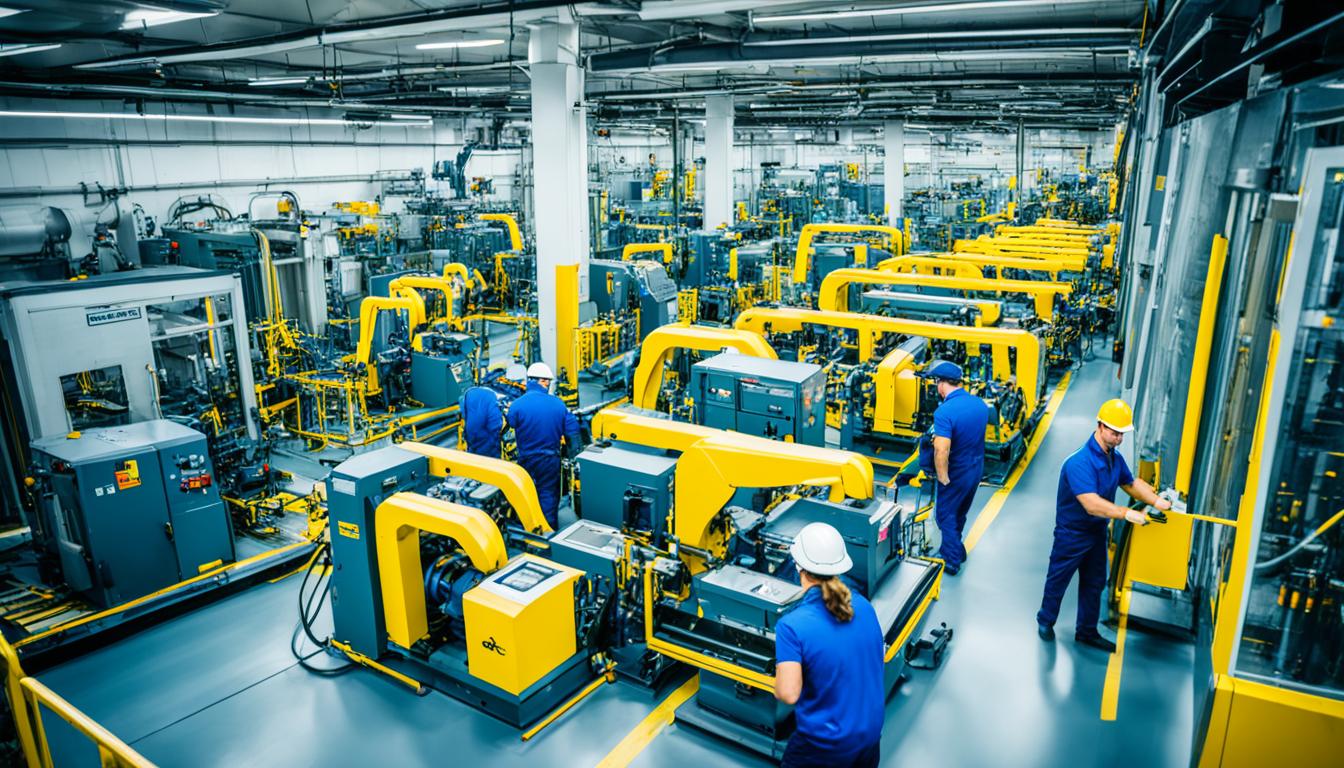
Capacity Utilization in Manufacturing
In the manufacturing world, knowing about capacity utilization is key to boosting your efficiency. This metric shows how much of your potential output you're actually reaching. By looking at capacity utilization, you can spot areas where your production could be better. This leads to using your resources more wisely.
A high utilization rate means your manufacturing is efficient and effective. It can also make your business more profitable, cut costs, and please customers by delivering on time.
Learning about the value of effective capacity utilization shows how important it is. Strategies like condition monitoring help make better maintenance choices. We'll look at what affects capacity utilization and how to make it better in the next sections.
Understanding Capacity Utilization and Its Importance
Capacity utilization is the ratio of what you actually make to what you could make, shown as a percentage. It's key for checking how well your manufacturing is doing and for managing resources better. Knowing about capacity utilization helps you see how efficient your operations are. This lets you use resources wisely and make production smoother.
The best capacity utilization rate is usually between 75% and 85%. This range helps you make products well and be ready for market needs. Staying in this range keeps you from making too much or too little, which is good for your business.
Low capacity utilization can mean paying more for each item made because costs are spread thin. On the other hand, using too much capacity can wear out equipment and make production less efficient. This shows why finding the right balance is so important.
Knowing and watching capacity utilization is key to smart resource management. It helps you make better decisions and improve how you make things. This knowledge is vital for overcoming challenges and doing well in manufacturing.
Key Factors Influencing Capacity Utilization
In manufacturing, many things affect how well you use your capacity. How you schedule production is key. It decides how you use your resources well. Good scheduling means smooth operations and fewer delays, making things more productive.
Using Predictive Maintenance can really help your efficiency. It lets you fix equipment before it breaks down, so you don't stop production. This way, you use your capacity better.
How well your workers do their jobs also matters a lot. A skilled team can handle changes fast, making your production better. Companies that train their workers often see their capacity go up.
Being able to change what you make easily is important too. If you can switch to different products or adjust to demand changes, you use your capacity better. This flexibility is key for keeping up with market changes.
Things outside your control, like changes in demand or competition, also affect you. For example, a big increase in orders can lead to using too much capacity. On the other hand, a drop in demand can mean not using enough resources.
Knowing about these factors is crucial for making the most of your capacity in manufacturing. Here's a quick look at the main influences:
Strategies to Improve Capacity Utilization
To boost capacity utilization, it's key to look into effective manufacturing strategies. One top method is using Lean manufacturing. This approach cuts down on waste and boosts productivity, making operations more efficient.
Regular checks on capacity help spot where production might slow down. By doing these audits, you can look at workloads, check how equipment is doing, and see how workflows work. This shows where you can get better.
Adding new technology can really help your manufacturing plans. Automation and smart systems help with forecasting and making production schedules more flexible. This tech helps use capacity better by quickly adjusting to new demands.
Building a culture of always getting better is crucial for better operations. Encouraging your team to come up with new ideas can lead to more efficiency and smarter use of resources.
Benefits of Optimizing Capacity Utilization
Optimizing capacity utilization brings many benefits to your manufacturing process. It lowers production costs per unit, which helps improve your profits. By using your equipment and workforce fully, you see more efficiency and financial gains.
This efficiency leads to happier customers. You can meet deadlines and keep products in stock, making you more reliable. This builds a strong reputation and keeps customers coming back.
Also, managing resources better means less equipment downtime. This means you can plan better for the future. A good strategy makes your business more efficient, agile, and ready for changes in the market.