Criticality Analysis
Criticality Analysis is a systematic process used to evaluate and rank assets based on their criticality to operations, safety, and overall business objectives. This analysis considers factors such as the likelihood of failure, the consequences of failure, and the asset's role in production. The outcome helps organizations prioritize maintenance activities, allocate resources effectively, and optimize maintenance spending.
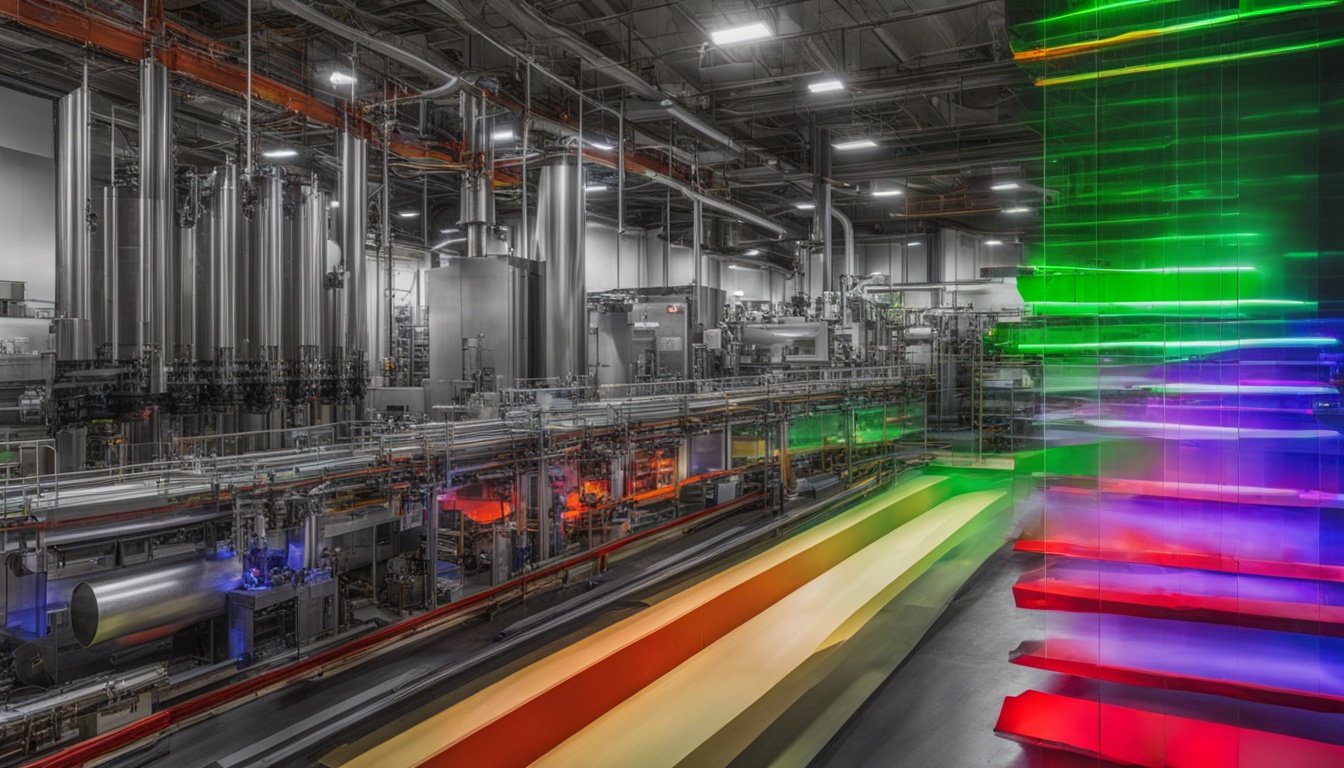
Criticality Analysis in Manufacturing
Do you know how big a role Criticality Analysis plays in making manufacturing better? It's a way to see which assets in your place are most important. By figuring out how each piece of equipment helps with your work, you can focus on what needs the most maintenance. This makes your manufacturing more efficient.
Understanding Criticality Analysis means seeing how losing an asset affects production and safety. This can really change how profitable and reliable your company is. Many companies use it to work better, cut down on downtime, and use resources wisely. Adding Criticality Analysis to your operations could change the game for you too.
Understanding Criticality Analysis in Manufacturing
To understand criticality analysis definition, it's key to see its role in manufacturing. This method helps businesses figure out which assets are most important for success. It looks at how an asset works, its maintenance costs, and what happens if it fails. This way, companies can use their resources better and focus on what's most critical.
Asset criticality analysis sorts equipment by importance. It shows which ones need quick attention. This helps lower risks and make operations smoother. Knowing which assets are critical lets companies use their resources wisely, boosting productivity.
Condition Monitoring tools like vibration analysis and thermal imaging are key for keeping critical equipment running well. They give real-time info on how assets are doing. This lets you spot problems early, avoiding big downtime costs. Moving to a proactive maintenance plan with solid data makes your assets work better and last longer.
Putting a big focus on criticality analysis and its methods can change how you do maintenance. By adding these practices to your routine, you start moving towards better performance and more reliable assets.
Implementing Criticality Analysis for Efficient Maintenance
Effective maintenance plans rely on criticality analysis. Start by identifying critical assets. This means knowing which equipment is key to your manufacturing. It helps put resources where they're most needed.
Then, sort equipment by how critical it is. This helps your team know what to fix first. Using prescriptive maintenance saves money and optimizes resources. Preventative maintenance is also key, fixing problems before they get worse.
Use tools like Condition Monitoring systems to keep an eye on your assets. This supports predictive maintenance by showing you the real-time health of your equipment. With this info, you can plan maintenance better, cutting down on downtime and keeping important machines running.
The Role of Criticality Analysis in Predictive Maintenance
In manufacturing, combining criticality analysis with predictive maintenance is key. It boosts asset reliability and makes operations more efficient. Predictive maintenance lets you spot potential equipment failures before they happen. This is thanks to advanced data analysis and monitoring tools.
Techniques like vibration analysis and temperature sensors give crucial data. When used with criticality analysis, they help pinpoint which assets need quick attention. This way, you can focus on what's most important.
Using criticality analysis helps you decide where to put your maintenance efforts first. Some assets might need quick fixes, while others can wait. This smart approach saves resources and time. It also uses data to make informed decisions, cutting down on equipment downtime and boosting performance.
Many industries have seen big gains by using these methods together. By merging criticality analysis with predictive maintenance, companies can make their equipment last longer and work better. This teamwork makes operations smoother, cuts costs, and increases reliability. It helps you stay competitive in the market.