Non-Destructive Testing (NDT)
Non-destructive testing (NDT) encompasses a variety of analysis techniques used in science and industry to evaluate the properties of materials, components, or systems without causing any damage. NDT is crucial for maintenance and reliability, as it enables the detection of defects and irregularities in equipment while preserving its usability. Common NDT methods include ultrasonic testing, magnetic particle testing, liquid penetrant testing, radiographic testing, and eddy current testing. These techniques help ensure the safety, performance, and longevity of critical assets.
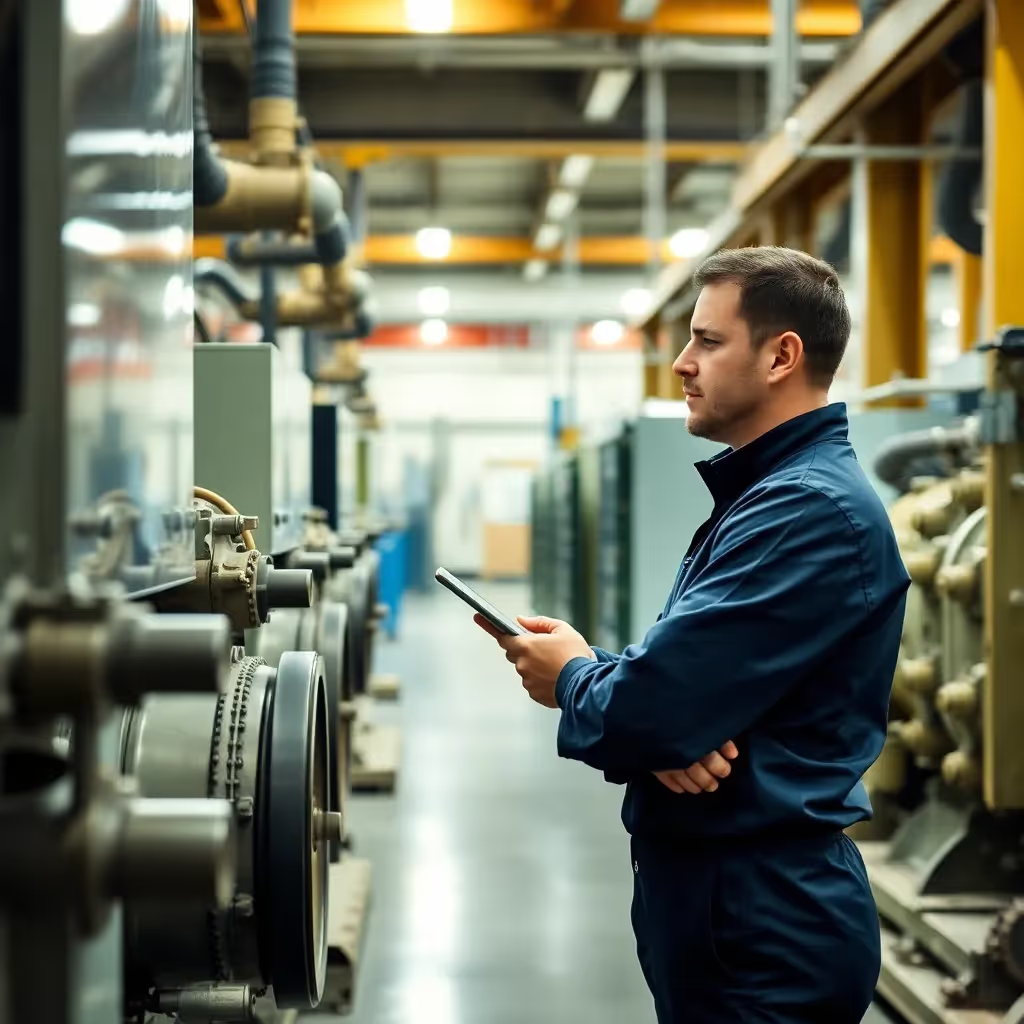
Key Takeaways:
- Non-Destructive Testing (NDT) evaluates materials without causing damage.
- NDT is crucial for condition monitoring and preventive maintenance.
- Techniques like ultrasonic testing and radiographic testing are commonly used.
- It can be applied across various industries, not just high-risk sectors.
- Integrating NDT with vibration analysis enhances predictive maintenance strategies.
Non-Destructive Testing (NDT) refers to a group of techniques used to evaluate the properties of a material, component, or system without causing any damage. This testing method is crucial in the maintenance industry, as it allows for the assessment of structural integrity and performance while preserving the item's usability. Common NDT techniques include ultrasonic testing, radiographic testing, and magnetic particle testing, all of which provide valuable insights into the condition of equipment and materials, ultimately enhancing safety and reliability.
Incorporating NDT practices within a broader maintenance strategy can significantly boost the effectiveness of condition monitoring and preventive maintenance efforts. For instance, regular NDT inspections enable technicians to detect potential failures before they escalate, aligning with predictive maintenance strategies that utilize data analysis to forecast equipment performance. This proactive approach not only extends the lifespan of machinery but also reduces unexpected downtimes and repair costs, making NDT an essential component of modern maintenance practices.
A common misconception about NDT is that it may only be necessary for high-risk industries, such as aerospace or nuclear power. In reality, NDT can benefit virtually any sector that relies on machinery or structural elements, from manufacturing to transportation. For example, vibration analysis can be integrated with NDT to monitor machine performance, helping to identify misalignments or imbalances that could lead to costly failures. By leveraging both NDT and other maintenance strategies, organizations can foster a safer and more efficient operational environment.