Operational Technology (OT)
Operational Technology (OT) involves the use of hardware and software to monitor and control physical processes, devices, and infrastructure. In the context of manufacturing, OT is crucial for managing and optimizing industrial operations, ensuring safety, and supporting predictive maintenance practices through real-time data collection and analysis.
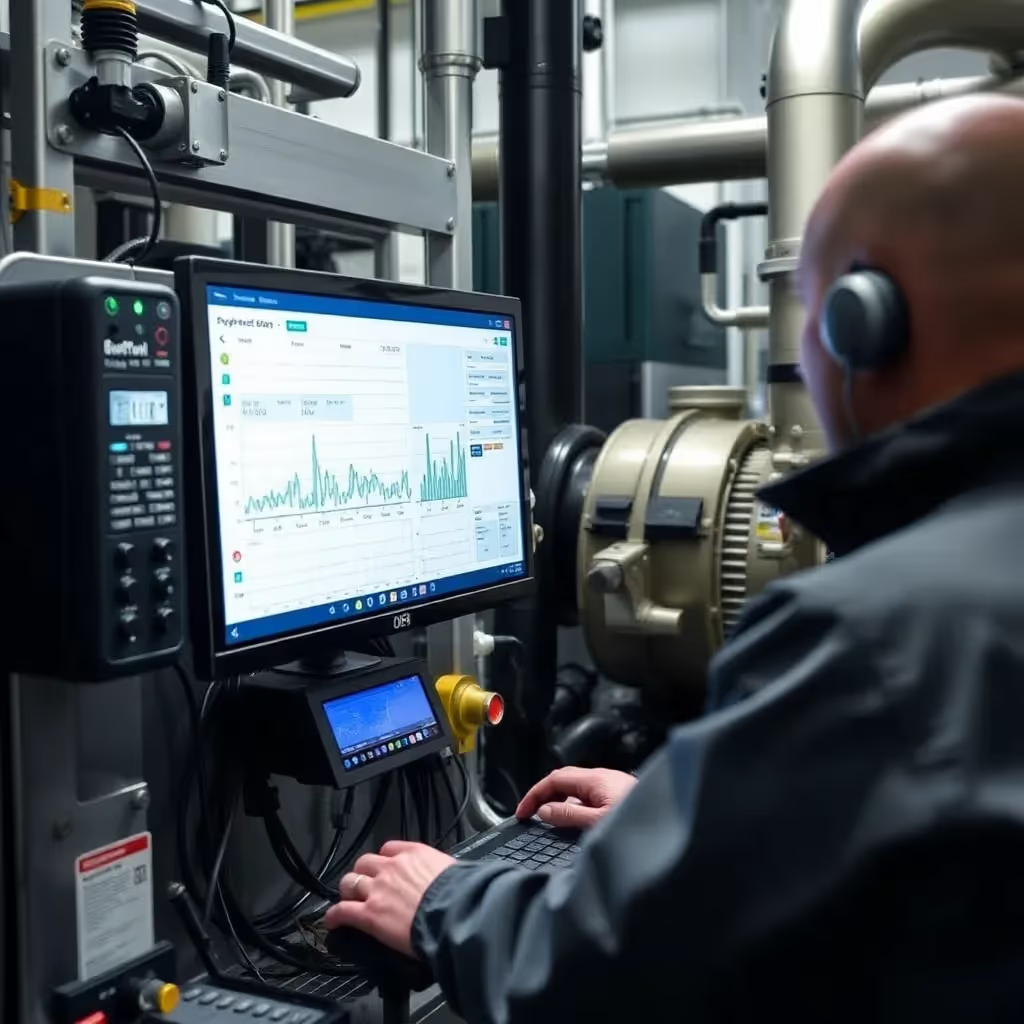
Key Takeaways
- Operational Technology (OT) focuses on monitoring and controlling physical processes in the maintenance industry.
- It closely relates to Condition Monitoring and Predictive Maintenance, enhancing equipment reliability.
- Misconceptions about high initial costs can overshadow the long-term benefits of adopting OT.
- OT promotes proactive maintenance strategies, improving overall operational efficiency and safety.
Operational Technology (OT) refers to the hardware and software that detects or causes changes through direct monitoring and control of physical devices, processes, and events in the maintenance industry. OT is integral to various sectors, including manufacturing, energy, and transportation, where it helps optimize operations, enhance safety, and improve efficiency. As the landscape of industry evolves with the rise of smart manufacturing and the Industrial Internet of Things (IIoT), understanding OT becomes crucial for professionals aiming to streamline processes and leverage technology in maintenance practices.
A key aspect of OT is its relationship with Condition Monitoring and Predictive Maintenance. Condition monitoring involves real-time assessment and feedback on equipment performance, enabling teams to identify potential failures before they occur. This proactive approach is coupled with predictive maintenance, which utilizes data analytics and historical performance metrics to forecast equipment health and schedule timely interventions. Together, these elements of OT provide a solid foundation for maintaining operational efficiency, reducing costly downtimes, and ensuring that maintenance tasks are performed based on actual equipment conditions rather than arbitrary schedules.
In practice, many companies still struggle with misconceptions about OT, often underestimating its potential impact on maintenance operations. For example, some believe that investing in OT leads to high initial costs without immediate returns. However, the long-term benefits of reduced downtime, enhanced safety, and improved asset utilization typically outweigh these concerns. Furthermore, integrating OT into existing maintenance strategies promotes a shift from reactive to proactive approaches, ultimately driving performance improvements and cost savings.