PFMEA
Process Failure Mode and Effects Analysis (PFMEA) is a systematic approach used to identify potential failure modes in a process and assess their impact on product quality and operational efficiency. PFMEA helps in prioritizing risks based on their severity, occurrence, and detectability, and in implementing control measures to mitigate these risks. It is a valuable tool for improving reliability and quality in manufacturing and maintenance processes.
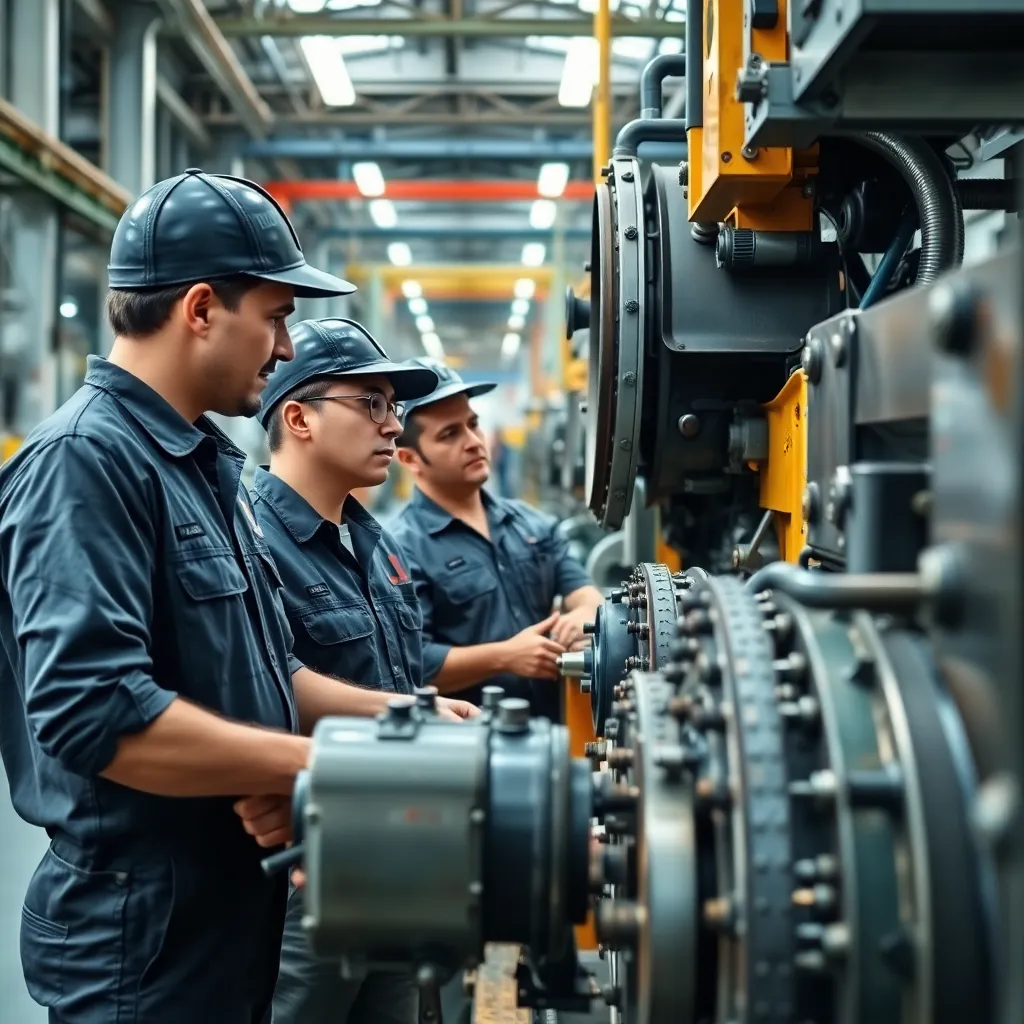
Key Takeaways:
- PFMEA is a proactive approach to identifying and mitigating potential process failures.
- Condition Monitoring enhances the effectiveness of PFMEA through real-time data.
- PFMEA is an ongoing process, not a one-time evaluation.
- Utilizing tools like Vibration Analysis can improve failure mode identification.
- PFMEA supports Preventive and Predictive Maintenance efforts in a maintenance program.
Process Failure Mode and Effects Analysis (PFMEA) is a systematic, proactive method used to identify and evaluate potential failure modes within a process and their associated effects. Developed initially in the automotive industry, PFMEA has since been adopted by various sectors, including manufacturing, healthcare, and aerospace. By conducting a PFMEA, organizations can prioritize risks associated with process failures, allowing them to develop effective strategies to mitigate these risks and enhance overall process reliability.
In the context of maintenance, Condition Monitoring plays a critical role in the PFMEA process. By continuously observing the state of equipment and systems, maintenance teams can identify signs of wear, degradation, or impending failure. This data can inform the PFMEA, enabling a more accurate assessment of potential failure modes and their effects. Additionally, PFMEA supports Preventive Maintenance efforts by helping organizations schedule maintenance tasks based on identified risks, thus reducing downtime and extending equipment life.
Common misconceptions surrounding PFMEA include the belief that it is only a one-time activity. In reality, PFMEA should be treated as an ongoing process that evolves with changes in equipment, technology, and operational conditions. For instance, utilizing Vibration Analysis can enhance the PFMEA by providing real-time data on equipment performance, thereby identifying failure modes earlier and allowing for timely interventions. Furthermore, Predictive Maintenance strategies can be powered by insights gained from PFMEA, leading to not only cost savings but also increased operational efficiency.