Unplanned Downtime
Unplanned downtime refers to periods when production or operations are unexpectedly halted due to equipment failure, system malfunctions, or other unforeseen issues. This type of downtime can lead to significant operational and financial impacts, including lost productivity, increased repair costs, and potential penalties for delayed deliveries. Minimizing unplanned downtime is a key focus of effective maintenance strategies.
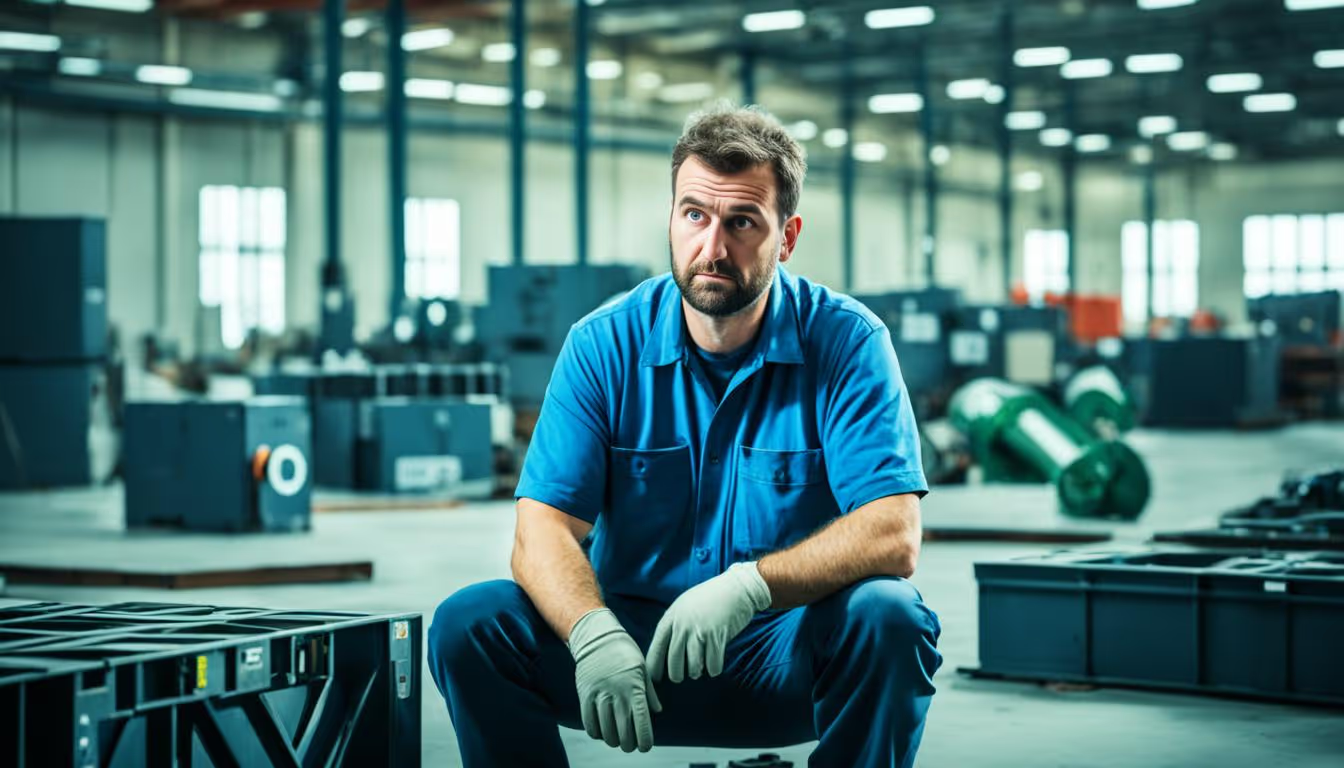
In the manufacturing world, unplanned downtime can really slow things down. These sudden stops hurt productivity and bring up costs. Often, it's because of equipment failure, maintenance issues, or things we didn't see coming. A study by the U.S. Department of Energy found that unplanned downtime can take up over 20% of your manufacturing time. This can really hit your wallet hard.
To keep your operations running smoothly, it's key to use smart strategies. Things like predictive maintenance and checking the condition of your equipment can help. By figuring out why downtime happens, you can make plans to avoid it in the future. This way, you can keep your production on track.
Key Takeaways
- Unplanned downtime significantly affects productivity and increases costs.
- Equipment failure is a primary cause of unplanned interruptions.
- Effective strategies like predictive maintenance can enhance operational efficiency.
- Understanding root causes is essential for developing effective downtime solutions.
- Mitigating unplanned downtime can lead to improved overall efficiency in manufacturing.
Understanding Unplanned Downtime
Unplanned downtime has many sides and reasons. A big cause is when equipment fails without warning, stopping work. Another reason is mistakes made by people, which can also stop work.
Nearly 80% of manufacturing downtime is linked to maintenance and human-related issues, as highlighted by the National Institute of Standards and Technology.
Using condition monitoring helps fight unplanned downtime. This method uses advanced tech to spot problems before they happen. By doing this, you can keep things running smoothly and lessen the bad effects of downtime.
Impact of Unplanned Downtime on Productivity
Unplanned downtime can really slow down manufacturing work. When machines break down or stop working, it causes big delays. These delays can hurt your efficiency a lot.
Businesses often lose money when production stops. Many manufacturing companies say they lose 5% to 20% of their productivity because of unplanned downtime. This loss affects profits and costs too.
Workers can get unhappy and less motivated during downtime. Long periods of not working can make them feel frustrated. This can make your manufacturing less efficient, which means you might not meet your quality and timing promises to customers.
Not fixing these downtime issues can hurt your business in the long run. Losing customer trust is a big problem. It's important to deal with downtime to keep your productivity up and your business successful.
Strategies to Minimize Unplanned Downtime
Fixing unplanned downtime needs a mix of good maintenance and monitoring. Using Predictive Maintenance is a smart way to act before problems start. It looks at real-time data to predict when equipment might fail. This lets you fix issues early, keeping things running smoothly.
Preventative Maintenance is also key. Regular checks and maintenance plans help stop sudden breakdowns. By looking at possible failure causes, you can cut down on unexpected downtime.
Condition Monitoring is vital too. Techniques like Vibration Analysis give insights into equipment health. This helps spot early signs of wear, guiding maintenance plans.
Advanced analytics can improve maintenance even more. With prescriptive maintenance, you get specific advice on what to do next. This lowers the risk of unplanned downtime. Using these strategies together makes your operations stronger against surprises.
Enhancing Operational Efficiency with Vibration Analysis
Vibration analysis is key to making your operations run better. It closely watches the vibrations of your machines. This helps you find mechanical problems early, before they turn into big issues. It's a big part of keeping an eye on your equipment's condition.
Putting vibration analysis at the heart of your maintenance plans leads to long-term success. It helps you catch problems early, keeping your equipment running smoothly. This means you can stick to your production schedule, setting your business up for growth and stability.