Uptime Improvement
Uptime Improvement refers to increasing the amount of time equipment is available and operational. In manufacturing, improving uptime directly correlates with increased production capacity, efficiency, and profitability. Strategies include implementing predictive maintenance, improving maintenance processes, and enhancing equipment reliability through regular monitoring and adjustments.
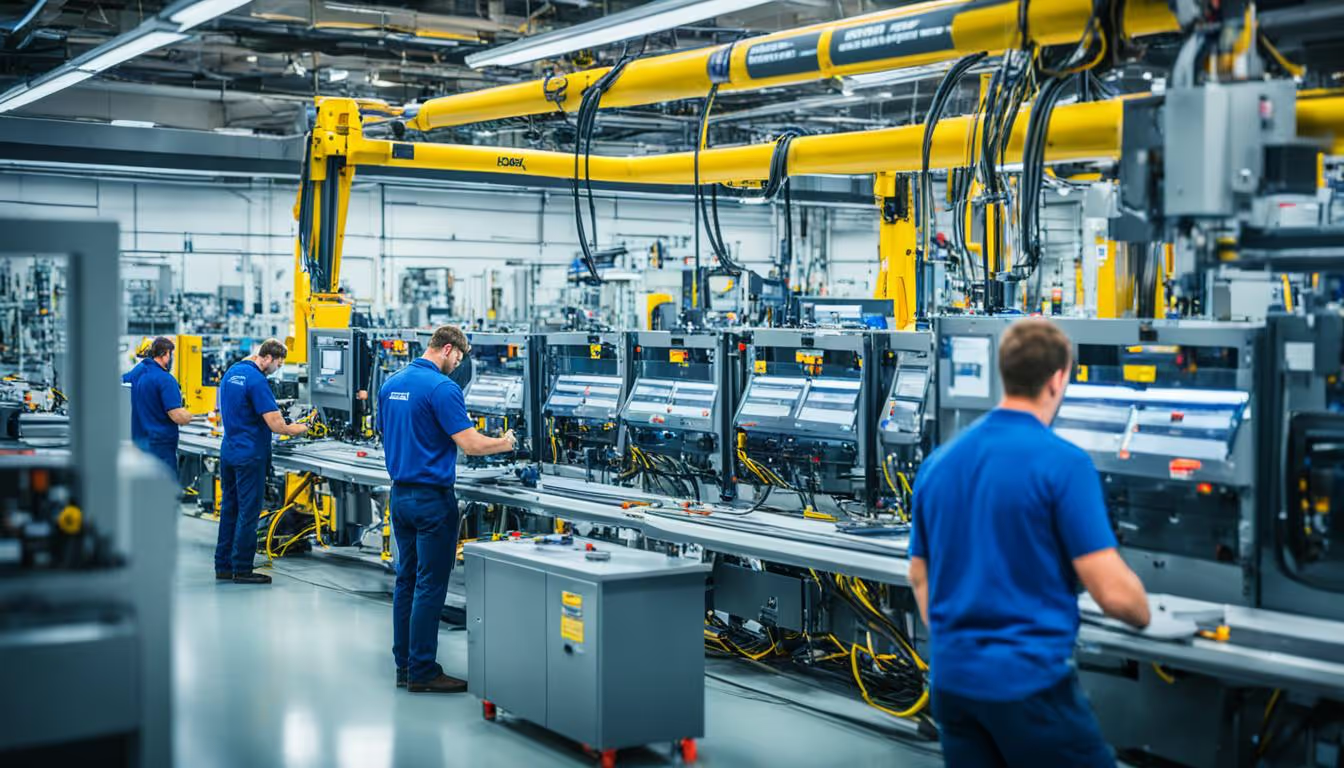
Uptime Improvement in Manufacturing
In today's fast-paced manufacturing world, keeping things running smoothly is key. Making sure your production is always up and running helps improve quality and get products out on time. With more competition, making sure your factory doesn't stop is more important than ever. This is because any lost time can hurt profits and make customers unhappy.
Studies show that unplanned stops can take up to 30% of production time. This fact shows how critical it is to find ways to keep things moving. By using new maintenance methods like predictive maintenance and checking equipment conditions, you can cut down on stops. This helps you stay ahead in the market.
Key Takeaways
- Uptime improvement is essential for maximizing manufacturing efficiency.
- Reducing downtime can enhance profit margins and customer satisfaction.
- Unplanned downtime can consume up to 30% of production time.
- Investing in predictive maintenance can lower the risk of equipment failures.
- Condition monitoring is vital for proactive maintenance strategies.
The Importance of Uptime Improvement in Manufacturing
Understanding the importance of uptime improvement is key to making your manufacturing operations run smoothly. Downtime can come from equipment failures, supply chain issues, or workforce problems. Every minute of downtime hurts your productivity and increases costs.
Studies show that unplanned downtime can cost manufacturers billions each year. This highlights the need to improve machine availability. With the move to Just-In-Time (JIT) production, constant efficiency is crucial.
Improving uptime helps cut costs and boosts productivity. Companies that use advanced maintenance see big gains in uptime. This leads to a more agile and profitable manufacturing setup. Focusing on these practices also helps the industry stay sustainable over time.
Strategies for Uptime Improvement
Improving uptime is key for your manufacturing success. By focusing on preventative, predictive, and condition monitoring maintenance, you can boost productivity and cut downtime.
Preventative maintenance means regular checks and upkeep to stop problems before they get worse. This way, you can make your equipment last longer and avoid sudden breakdowns.
Predictive maintenance uses data and learning to predict when equipment might fail. This lets you fix things before they break, saving time and money.
Condition monitoring keeps your equipment running well. With tools like vibration analysis and thermal imaging, you can check on your machines all the time. This helps you find and fix problems fast, keeping your production smooth.
- Regular inspections and routine servicing are key components of preventative maintenance.
- Data-driven insights are fundamental in predictive maintenance approaches.
- Condition monitoring technologies help maintain optimal equipment performance.
Using these strategies can make your manufacturing more efficient and reliable.
Uptime Improvement: Tools and Technologies
In today's fast-paced world, using advanced tools and technologies is key for better uptime. Uptime Improvement Technologies are changing old ways, bringing new solutions that make production better.
Smart manufacturing uses the Internet of Things (IoT in Manufacturing) to make things smoother. With real-time data, you can make smart choices that boost efficiency. Predictive analytics software uses big data to see and fix problems before they happen, saving time and money.
Companies like Siemens and Honeywell lead the way with their advanced solutions. These solutions use artificial intelligence to make maintenance schedules better. This makes equipment more reliable and cuts down on unexpected downtime.
- Real-time data analysis for quick decision-making
- Predictive analytics to identify production bottlenecks
- AI-powered solutions to improve maintenance schedules
- Integration of Smart Manufacturing techniques for efficiency
Using these Uptime Improvement Technologies can change how your organization makes things. It leads to more uptime, and makes your company more agile and quick in a fast-changing market.