Vibration Monitoring
Vibration Monitoring is a technique used to detect abnormal vibrations in machinery that could indicate mechanical issues, such as imbalances, misalignments, or bearing failures. By continuously measuring vibration levels, it provides early warning signs of equipment deterioration, allowing for timely maintenance or adjustments. Vibration monitoring is a critical component of condition-based maintenance programs, helping to prevent unexpected equipment failures.
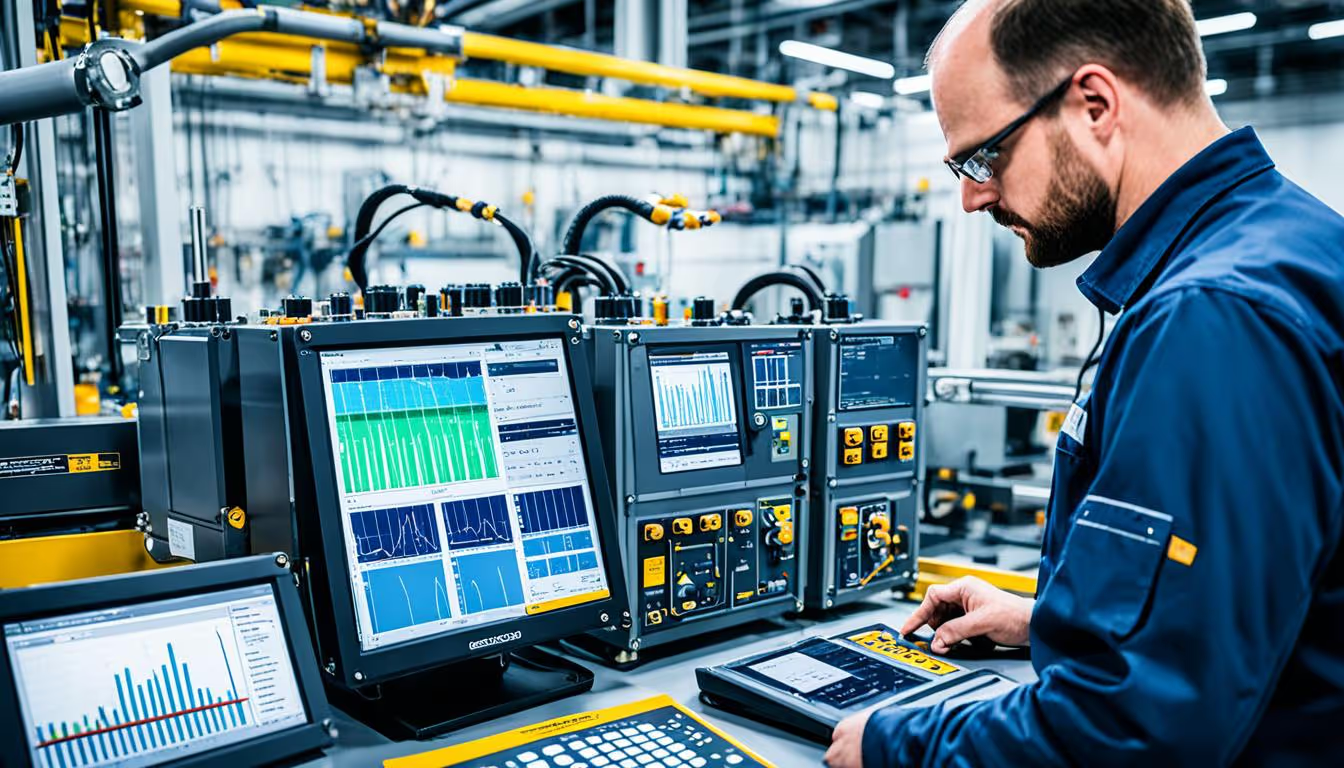
Vibration Monitoring in Manufacturing
In the fast-paced world of manufacturing, keeping your machinery running smoothly is key. Vibration Monitoring helps you do just that. It lets you check and analyze the vibrations from your equipment. This way, you can spot problems before they cause big delays, saving you money and time.
Using vibration monitoring systems is a smart move. It helps you keep up with Condition Monitoring and Predictive Maintenance. This means your equipment stays in top shape, and you spend less on sudden repairs.
When you dive into Vibration Monitoring, you'll see how important sensors and data systems are. They help you track how well your equipment is doing over time. With this info, you can take steps to keep your equipment running well and make it last longer. Let's dive into how vibration monitoring changes the game for manufacturing.
Key Takeaways
- Vibration Monitoring is key to keeping your equipment reliable.
- These systems help with efficient Condition Monitoring.
- Being proactive leads to better Predictive Maintenance.
- Using data can stop costly downtime.
- Special sensors and tools are vital for tracking performance.
- Good Preventative Maintenance can make your equipment last longer.
Understanding Vibration Monitoring
Vibration Monitoring is key to checking how well rotating machines and equipment work. It measures the vibrations these machines make. This helps you understand their condition.
By using Vibration Analysis, you can spot early signs of wear or problems. This means you can fix things before they break down, saving time and money.
Many machines like pumps, motors, turbines, and compressors benefit from Condition Monitoring. Regular checks with vibration data keep them running well and last longer. Knowing how vibrations show the health of your equipment is crucial for smooth operations.
To use Vibration Monitoring, you need sensors that catch the vibrations. These sensors send data about the vibrations' frequency and size. This data is then analyzed to find any odd patterns in the equipment's work.
Knowing what normal vibrations look like helps you spot any problems early. This leads to better maintenance and fewer unexpected breakdowns.
Adding Vibration Monitoring to your maintenance routine makes your machines more reliable. It also saves you money over time. As you get better at reading vibration data, you can prevent equipment failures. This builds a culture of doing things right and being sustainable.
Benefits of Vibration Monitoring for Manufacturing
In the fast-paced world of manufacturing, Vibration Monitoring is key to keeping things running smoothly. It brings many benefits that change how you care for your machines.
One big plus is how it boosts Predictive Maintenance. By keeping an eye on equipment vibrations, you can spot problems before they happen. This means you can fix things early, cutting down on unexpected stops. Your machines work longer and better, making your production flow better.
- Cost Savings: Reduced maintenance and repair costs by preventing failures.
- Operational Efficiency: Enhanced overall productivity due to less downtime.
- Improved Safety: Decreased risk of accidents related to machinery failure.
Vibration Monitoring also gives you Prescriptive Insights. This lets you make smart choices based on data. By looking at vibration data, you can improve your operations, plan maintenance better, and spend wisely on upgrades. This smart planning boosts productivity and puts your company ahead in the market.
Putting money into Vibration Monitoring systems helps you always get better. With technology, you can follow best practices. This keeps your operation flexible and ready for new challenges.
Implementing Vibration Monitoring in Your Facility
Starting with Vibration Monitoring in your facility means first checking your equipment. Look for machines that are key to your work. This helps you focus on machines that need Condition Monitoring the most.
After picking out these important machines, you need to choose the right Vibration Monitoring tech. You might look at handheld analyzers, ongoing monitoring systems, or wireless sensors. Each has different levels of data collection and analysis, based on what you need and can afford.
Then, make a detailed plan for how to use the monitoring solution. This plan should cover who will do the monitoring, how often data will be checked, and how it will be analyzed. Getting maintenance teams involved helps them understand and take part in the new process.
Checking the data regularly is key. This keeps your Preventative Maintenance plan strong. By looking at trends, you can spot problems early, avoiding big downtime costs. Also, make sure your team talks about what the data shows to share insights and findings.
Setting up Vibration Monitoring is an ongoing process, not just a one-time thing. Keeping an open conversation about what works and what doesn't will make your monitoring better. This helps keep your facility running smoothly and reliably.
Future Trends in Vibration Monitoring
The world of vibration monitoring is changing fast, thanks to new technology. Soon, the Internet of Things (IoT) and Artificial Intelligence (AI) will change how we manage equipment. IoT devices will collect lots of vibration data in real-time. This means you can keep an eye on your equipment's condition all the time.
AI will also make predictive maintenance better. It will look at data from different machines to predict when they might break down. This way, you can fix problems before they happen, cutting down on downtime and repair costs. It helps your manufacturing run better and more efficiently.
Future tech will bring even better data analysis and reporting to vibration monitoring. By using these new tools, you can stay ahead in your field. You'll move from old ways to a new approach focused on making things reliable and productive.