Zero Waste Manufacturing
Zero waste manufacturing is an approach focused on minimizing waste production through efficient processes, recycling, and the sustainable use of resources. It aims to eliminate all forms of waste in the manufacturing process, including material scraps, energy use, and time. Maintenance plays a crucial role in zero waste manufacturing by ensuring equipment operates efficiently, reducing unnecessary consumption of resources, and supporting sustainability initiatives.
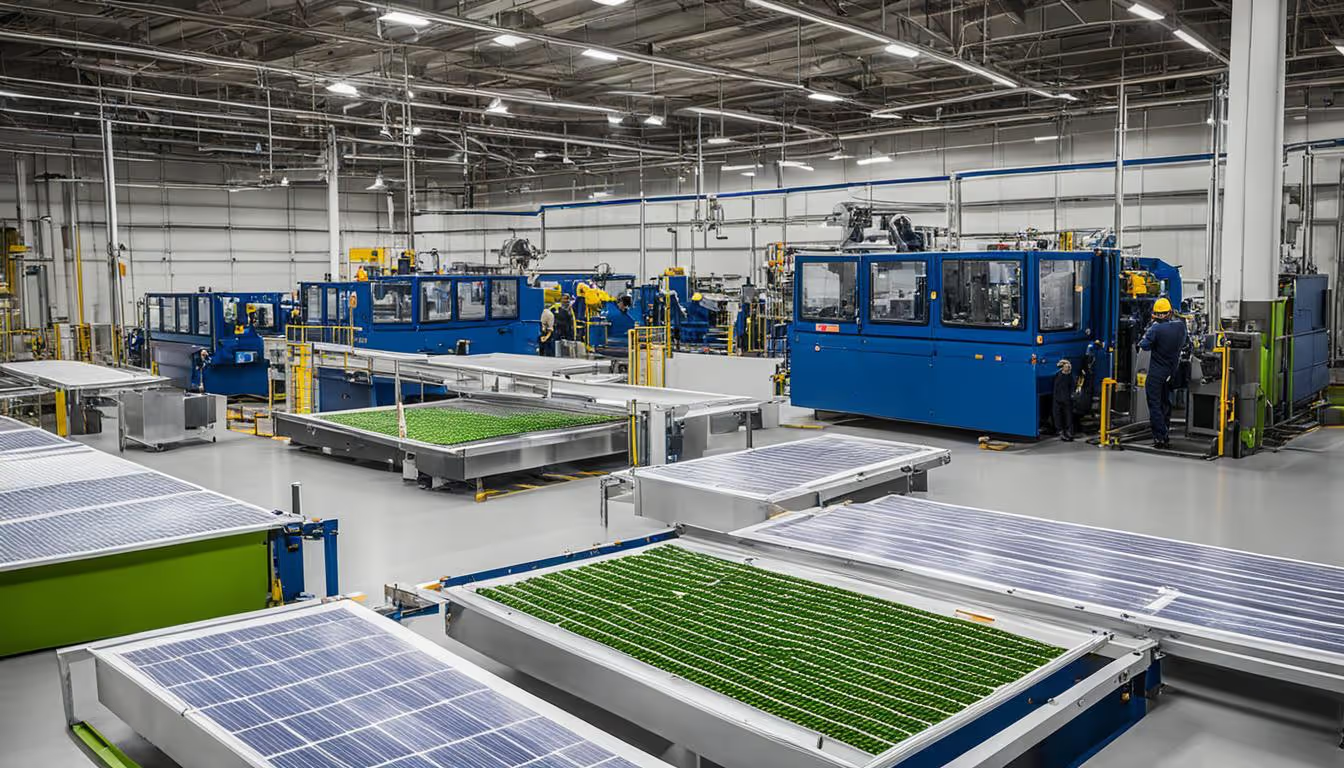
Zero Waste Manufacturing
Welcome to the world of Zero Waste Manufacturing. This approach aims to get rid of waste in the production process. By going eco-friendly, you boost efficiency and help the planet. It also meets the needs of customers who care about the environment.
Companies have seen big benefits from zero waste. They've improved their production and taken steps towards sustainability. The Ellen MacArthur Foundation says going zero waste can save money and open up new chances for business.
Key Takeaways
- Zero Waste Manufacturing minimizes waste and enhances operational efficiency.
- It aligns with environmental regulations and consumer expectations.
- Transitioning to zero waste can lead to cost savings and new opportunities.
- This approach aids in achieving sustainable success through eco-friendly production.
The Importance of Zero Waste Manufacturing
Zero Waste Manufacturing is key to making industries more sustainable. It aims to reduce waste by reusing, recycling, or composting materials. This approach helps companies lower their environmental impact and improve their financial health.
Manufacturing is a big source of global waste. Using Zero Waste methods helps fight pollution and save resources. By cutting down on waste, companies can keep materials out of landfills and support a circular economy.
Being committed to sustainability can also make your brand more appealing. Many customers want to support companies that care for the environment. By focusing on Zero Waste, you can stand out and gain loyal customers.
Switching to Zero Waste can also open up new ways to make money. By recycling and reusing materials, you can turn waste into valuable resources. This gives you a unique edge in your industry.
Innovative Strategies for Achieving Zero Waste Manufacturing
To reach Zero Waste Manufacturing, we need new strategies. One key approach is using condition monitoring. This helps spot equipment problems before they cause big issues. Techniques like vibration analysis give us important clues for better waste management.
By fixing problems early, we can cut down on waste and work more efficiently.
Lean manufacturing is another way to reduce waste. It focuses on making the most value with fewer steps and less material. Companies like Tesla show how smart waste reduction can lead to success. They keep improving their ways to be more sustainable.
Using new tech like automation and real-time data analytics can boost your waste management. These tools help us make better processes, use less material, and help our planet. It's important to keep improving and innovating in your team. This keeps your company moving towards zero waste in manufacturing.
Prescriptive Maintenance vs. Predictive Maintenance
In today's manufacturing world, knowing the difference between Prescriptive and Predictive Maintenance is key. Predictive Maintenance uses data to predict when equipment might break down. This way, you can fix problems before they happen, cutting down on waste and improving efficiency.
Prescriptive Maintenance is more proactive. It uses advanced algorithms to suggest the best maintenance steps. This ensures your equipment runs well, lasts longer, and works more efficiently. By using these strategies, you can reduce downtime and waste.
Using both Prescriptive and Predictive Maintenance helps your company be more sustainable. You can reach your sustainability goals while lowering maintenance costs and increasing productivity. Adopting these methods puts you ahead in the game of zero waste manufacturing.